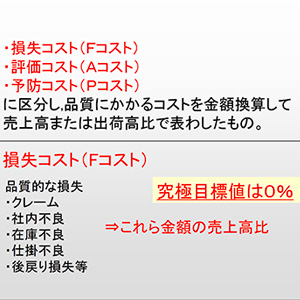
動作の無駄
次に、非常に多くの改善事例のある、また改善効果の高い「動作の無駄」について説明する。
動作の無駄とは、直接的に価値を付加しない人や設備の動きに関係する無駄のことである。たとえば、工具を置き間違えたために、作業者が工具を探すのに費やした時間などが動作の無駄にあたる。
付加価値を生まない動き、不必要な動きは、すべて直接付加価値を生む「働き」にはならないため、動作の無駄として扱うことが多い、といえる。
具体的には、探す、しゃがむ、持ち替える、調べるなどの人の動きの中で付加価値を生んでいない不要な動きであり、標準作業が誰でも同じようにできるようになっていない場合や、技能訓練不足などで発生しやすくなる。
つね日ごろから動作を観察し、付加価値を生んでいない動きがないか探していると、必ず動作の中に無駄が存在していることに気付くはずである。
動作の無駄を探すために、人の動きやものの動き、それらを単位で確認してみよう(図6)。
そして、発見した動作の無駄は、「省人化」に繋がるものなのか、それとも、「生産性を向上」させるものなのか、ということを明確に分け、作業標準化の改定に努めることをおすすめする。
動作の無駄は、
●人員や工数の増加
●技能の隠ぺい化
●作業の不安定性
●不要の動作
などが代表的であるが、原因としては、離れ小島作業、職人気質の蔓延、不適切なレイアウト、教育や訓練不足が一般にあげられる。
であるので、一般論としての対策は
●流れ生産への組み込み
●U字型設備配置化
●「表準作業」の標準作業化
●「動作経済の原則」の徹底
などが対策としてあげられます。
動作の無駄について改善を望むのであれば、よくよく観察してみることである。すると、様々な人の動きが見えてくる。たとえば…
1. 歩行をしている時間
作業台から次の作業台へ物を持って移動している時、部品置き場への移動や一般的に現場で働く作業者は、1日に5,000?15,000歩以上歩いているといわれている。この1歩が1秒としても5,000?15,000秒もの時間を費やしていることになるのである。1日の約半数以上はこの時間にあてはまる、という工場も少なくないと思う。
では、この原因は何か? 工程と工程が離れているからだろうか? 作業台と作業台が離れているからだろうか? 工場によって様々だと思う。
「同じ生産数を基準として、昨日よりもどれだけ歩行が減ったのか?」を改善によって減少させることが、生産性を一番早く改善できる方法の一つにもなる(※「部分最適化」という言葉のもとに、設備のタクトのみをきにする企業が多いのが残念である)。
現場の人は1個作るためにどれだけ歩行しているのか、そしてそれは付加価値が付いているのか、を判断しながら、さっそく現場を観察してみよう(図7)。
2. 手を動かしている時間
皆さんも、作業台などの上で工具を取ったり、部品を取ったりするであろう。これも作業者としてはあたりまえの作業として行っているので、工場でよく見かける風景だと思う。
では、50センチ離れた所から工具を取る作業者と、10センチ離れた所から工具を取る作業者では、どちらの生産性がいいだろか?
この2人の作業者がともに1日100個生産している工程ならば、
●50センチ × 100個 = 5,000センチ
●10センチ × 100個 = 1,000センチ
と、換算してみるとかなり大きな数字になってしまう。
動作の無駄取り改善では、20センチ=約1秒と考えることが一般的なので
●5,000センチ = 250秒/日
●1,000センチ = 50秒/日
このような1点の改善だけで貴重な時間が短縮できることになる。現場の各地で行われている動作に目を向けると、生産性も大きく変わってくるのである。
3. 手待ちをしている時間
工場には自動機がたくさん並んでいる。特殊な加工技術などを行い、人間の手では時間がかかる作業を、機械が替りに作業していると考える。その時間に作業者は機械が加工している風景を眺めていても、決して良い製品ができるわけではない。このように加工できるまでに待っていることを「手待ち」という。
この例以外にも、2人作業で行っている作業で1人が準備している際に、相方を待っているのも「手待ち」にあてはまる。現場の作業者はこれらのように、生産するために様々な「無駄」を発生させながら生産しているのである。
そこで、この「動作の無駄」に目を向けて、人の能力を最大限に発揮した工場を作り上げることが必要になる。同様に、目線を外したり、持ちかえ作業による動作の増加行為は無駄である。
「無駄に気付く感性」を高める
というわけで、「無駄を無くすこと」は大事なことである。しかし、「時間を無駄にしない = 休まず動き続ける」ということでもない。
無駄を作っちゃいけない ⇒ スケジュールに空白を作らないようにしよう ⇒ スケジュールを埋めるための仕事を作り始める、なんてことになってしまっては笑い話になってしまう。
「無駄な仕事を作る」こと自体が無駄であるから… というわけで、「時間を無駄にしない = 動き続ける」というわけではなく、「動く中身の中に無駄が潜んでいないか?」と気づくことの方が大事なわけである。これは「無駄に気づく感性」という言い方がしっくりくるように感じる。
なお、私はわりとそういう無駄に気づくほうであるが、これまで一緒に仕事をした人の中には、私以上に「無駄」に対して鋭い視点をもつ人もいた。そういう人は、理屈で考える以前に、直感的に「これは無駄だ」と判断しているように見えるところが多々ある。まさに「感性」である。
では、その「無駄に気づく感性」を高めるためにはどうすればいいかというと、私は以下の2つのアプローチが有効だと考えている。
① 「目的」を考えること・見失わないこと
その仕事(あるいは会社の仕事全体)の「目的」を考えることである。
たとえば、「その会議は何の目的で開催されているか?」が明確になると、会議運営を変えるアイデアも出てくる。
会議の目的が「○○について検討する」というのでは、明確になったとはいえない。もう一歩踏み込んで具体的に、「○○を次にどう進めるか決定する」、「○○についての承認を得る」のように、本来は会議には仕事を次に進めるためのステップとしての役割があるはずである。
中には「連絡」が目的の会議もあるが、それだけが目的の会議はメールに取って代わられ、少なくなりつつある。
その「目的を果たす」ことを中心に考えると、何が「無駄」か見えてくる(その会議を行うこと自体が無駄という場合もあるはずである)。
② 無駄が起こる「パターン」を知る
「無駄に気付く感性」を高める、もう1つのアプローチは、どんなところに(どんな形で)無駄が潜んでいるか知ること、を考えることである。
「無駄」にはいくつかのパターンがある。それを、「トヨタ生産方式」では、「7つの無駄」と呼んでいる。
ところが、8つめの無駄として、
●何もしない無駄(生産の機会・改善の機会を失う無駄)
があげられることもある(他に諸説ある)。
この「7つの無駄」にあてはまるものがないか? という視点で見てみると、職場の中にある無駄は、かなり見つけやすくなる。「あたりまえ」だと思っているところに、結構「無駄」は潜んでいるものである。
それに気付くためのきっかけやガイドライン、ケーススタディとして「7つの無駄」は役立つと感じている。そうしているうちに、「感性」に近い、直感的な判断もできるようになってくるというのが私の実感である。
※少しPRさせていただくと、当社のセミナーでは、この「7つ の無駄(+1)」を「ホワイトカラー業務(デスクワーク)版」に 置き換えたものを解説している。興味がある人は、メール でいただきたい。
- 会社名
- 実装技術信頼性審査協会、 STCソルダリングテクノロジセンター
- 所在地
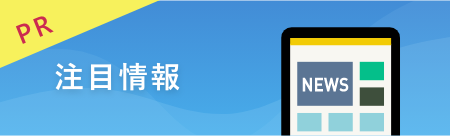
-
真空リフロー、N2リフロー、エアリフローのことなら、エイテックテクトロン(株)にお任せください。フラックスレス真空リフロー装置販売開始!エイテックテクトロン株式会社
-
独自の加工技術とノウハウで様々な材料にチャレンジ 〜色々なアイデアを生み出して研究者をサポート〜 ムソー工業株式会社 代表取締役 尾針 徹治 氏Gichoビジネスコミュニケーションズ株式会社
-
話題のGlass PKG実装技術の動向 〜先端電子部品への応用と 最新のCuダイレクトめっきGWCについて〜 Grand Joint Technology Ltd 大西 哲也(T. Onishi)Gichoビジネスコミュニケーションズ株式会社