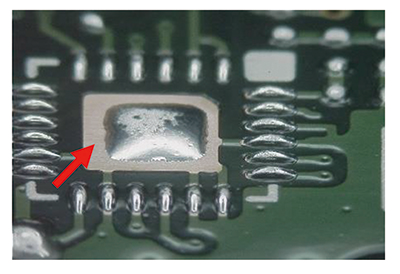
4. セルフアライメントの活用
上記の条件で、部品をずらして搭載し、リフロー時のセルフアライメント力を利用しガスをフィレット上からランドの外へ押し出す。なお、「 3 . 」 と本項「 4 . 」の手法は現場で一定の効果を得ている。 はんだ量が多ければ強いセルフアライメントが働きはんだ溶融前後に発生した気泡は部品によって押し出される(図 6)。
図6
5. 2度リフロー(図7)
ボイドの大きな要因はフラックスの溶剤などであるので、当該部品のみ1回目のリフロー時には部品を搭載しない。1回目のリフロー後、当該ランドにフラックスを塗布してから部品を搭載して再度リフローする。
1 回目のリフローではんだの溶剤が気化するため、ガスの発生量が減る。液状の薄いフラックスを塗布するが、大半が IPA のため、はんだ溶融前に低温で気化し、気泡として残らない。
特に糸はんだで予備はんだを行ったランドではボイドは完全に除去されている。 予備はんだをプリフォームはんだで代替するのも手である。
図7
6. 観察箇所
理論上、ボイドは基板上のすべてのポイントの観察が必要であるが、それではラインが止まってしまい、生産できない。 観察すべき部品は(図 8)、
① 部品下部にはんだ付け面(リード部)がある部品(QFN、 BGA、アルミ電解コンデンサ、水晶など)
② 発熱する部品
③ フラックスの劣化しやすい基板外側の部品
④ 基板上のスリット傍の部品
⑤ リード周りのフラックス残渣の荒れた部品
⑥ リード下のはんだ量が多い(厚い)部品
⑦ デンドライドや引け巣の多い部品
⑧ フィレット表面が滑らかでない、光沢がない
⑨ その他
図8
5.まとめ
以上の方法は現場でできる範囲であるが、これらを組み合 わせることで、 効果を高めることができる。 個々の対策では 効果が得られない場合もあるので、ライン固有の条件に合わ せて対策をとる。
いずれにしても、現場での対応では温度プロファイル、特に プリヒート部の熱量と下部ヒータの操作が基本になる。
- 会社名
- 実装技術アドバイザー
- 所在地
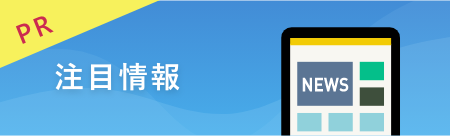
-
真空リフロー、N2リフロー、エアリフローのことなら、エイテックテクトロン(株)にお任せください。フラックスレス真空リフロー装置販売開始!エイテックテクトロン株式会社
-
独自の加工技術とノウハウで様々な材料にチャレンジ 〜色々なアイデアを生み出して研究者をサポート〜 ムソー工業株式会社 代表取締役 尾針 徹治 氏Gichoビジネスコミュニケーションズ株式会社
-
話題のGlass PKG実装技術の動向 〜先端電子部品への応用と 最新のCuダイレクトめっきGWCについて〜 Grand Joint Technology Ltd 大西 哲也(T. Onishi)Gichoビジネスコミュニケーションズ株式会社