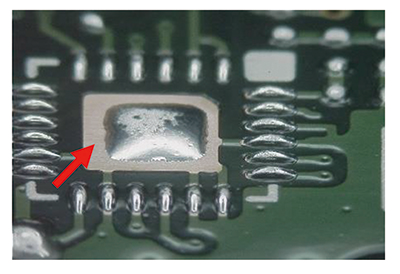
1.現場でのボイド対策
現在量産現場ではボイドについて、まだ十分な対策が取られていない。ボイドは通常の不良のようにインラインで外観観察して確認できるものでなく、一般的には実装後に1枚ず つ検査することになる。ボイドはすべてゼロにする必要はないが、部品リード側にある場合は品質問題につながる可能性が高い。基板ランド側にある場合は特に接合強度に大きな影響は与えない。ボイドに対する規格も一応あるが、一般論で個々の実装基板の使用環境を網羅してはいないので、その影響は使用される製品環境に合わせて検証する必要がある。単に規格数値内に収まればよいものではない。本来、立体構造 (cm3)であるボイドを平面(cm2)で規定するのは疑問だが、他に妥当な方法が見あたらない。生産技術的な対策として は真空リフローや蟻酸を用いた炉の導入が考えられるが、それぞれ一長一短があって現状では限定的なラインでの導入に留まっているようである。
2.ボイドの主な発生要因
ボイドは主に、はんだ付け時のガスがフィレット内部に残留したもので、部品下面の広いランド形状では気化しないフラックスの溶剤等が部品下に取り残されて大きなボイドが形成される。
① はんだのフラックス (樹脂+溶剤)
② 基板 (吸湿、ランド表面酸化)
③ 部品リード
④ 部品形状
⑤ 温度プロファイル
⑥ 設計
⑦ はんだの印刷形状
⑧ その他
現場での対応は、上記の②と⑤、及び⑦の項目くらいで他の条件はすでに確定され、変更することができないのが普通である。
3.現場での対応
実装基板の不良対策は、ボイドを含め、時間と投資負担を考慮してまずは現場で対応した後、改善が見られない部分について生産技術で対応・検討するのがよい。最初から技術対応を試みると、かなりの時間と投資が必要とされ、過剰な処置のわりに十分な効果が得られない場合が多い。特に、最近の日本(日系)の工場においては人的余裕がなく、現場の力が落ちていることから対応に遅れが目立っている。生産技術は主として理論やメーカーの協力を仰いで装置性能からの検証になるが、量産における問題は個々のラインにおける特殊性があり、当初の検証数値では把握仕切れない情報が隠れているのが普通である。メーカーは良品率99%、良くても99.9%であれば合格としているので、現場が要求するppmオーダーにはほど遠い。現場での対応では、完成品の良否の判定基準を明確にし、それに 合わせた結果を出してその後に規格に対応させると、比較的速く対処できる。現状は、規格を優先させるため、対応方法が制限され、不十分な結果で終わっていることが多いようである。
4.温度プロファイルでの対応
はんだ付け時、フラックスの樹脂や溶剤の一部が気化し、ガスが発生する。このタイミングで溶融はんだの流動性が十分であれば大半のガスはフィレットの外へ放出され、規格内に収まる。はんだの流動性はフラックス効果によるもので、フラックスを劣化させない温度プロファイルを用いればよい。
1. フラックスを劣化させないヒータ操作方法
① 基板下部からの加熱
印刷されたはんだに直接強い熱風を当てない
② プリヒート部の熱量(温度x時間)・熱風(ファンの回転数) を抑える
(注)フラックスの溶剤は 100 °C過ぎから軟化(流動化)し、 はんだの溶融段階では気化(ガス化)する。発生したガスははんだの熱対流でフィレット内部を移動し、一部はフィレット内部に留まるが、大半はフィレットの外へ放出される。図1の中のボイド(A)は、部品リードから直接熱を受け膨張収縮を繰り返し、強度に影響を与え、またリードの放熱を阻害する。同図中のボイド(B)は部品リードの熱はランドから基板へ放熱され強度への影響は小さい。
図1
- 会社名
- 実装技術アドバイザー
- 所在地
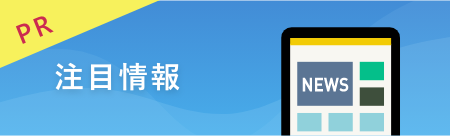
-
真空リフロー、N2リフロー、エアリフローのことなら、エイテックテクトロン(株)にお任せください。フラックスレス真空リフロー装置販売開始!エイテックテクトロン株式会社
-
アレムコの導電性/熱伝導性接着剤,コーティング材,グリースのことなら(株)エス・エス・アイ株式会社エス・エスアイ
-
独自の加工技術とノウハウで様々な材料にチャレンジ 〜色々なアイデアを生み出して研究者をサポート〜 ムソー工業株式会社 代表取締役 尾針 徹治 氏Gichoビジネスコミュニケーションズ株式会社
-
SEMICON Japan 2023 2023年12月13日(水)〜15日(金)の3日間、東京ビッグサイトにおいて、半導体を中心としたマイクロエレクトロニクスの製造を支える装置/材料産業の総合イベントであるSEMICON Japan 2023が開催された。Gichoビジネスコミュニケーションズ株式会社