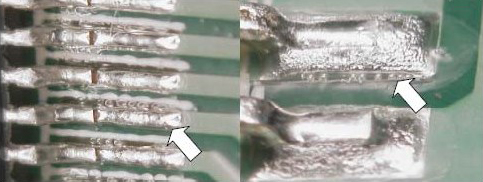
特に問題が起こった時は不良個所の写真は撮るものであろうが、同じ基板上における良品の写真の撮影を抜かしてしまいがちである。良品と判定しているものが不良品であればすなわち現場の問題である。そうでなければ部品または基板の問題ということになるので、必ず比較できる情報を、温度プロファイルと共にそろえて提出させる必要がある。
また、はんだ付け部の写真も撮り方が問題になります。はんだ付けはフラックスを使用する以上、そのフラックスの効果が最大の時はんだの接合強度も最適になるわけである。基板上において最初に熱反応を起こすのはフラックスで、約100?120℃程度で軟化しはじめる。そして溶けたフラックスは、リードやランドの熱に反応し、その周りにきれいな曲線を描く。たとえはんだ量が少なくても、適切に反応した場合は、はんだのフィレットとフラックス残渣は曲線(弧)を描くものである。外観観察の写真としてはこのフラックス残渣の形状とフィレットの接合界面を、斜め方向(時計の4時?5時、7時?8時、及び3時または9時方向)から捉えたものが必要である。また、コネクタやQFP・SOPなどでランドやそばにホールがある場合には、パターからの熱移動を判断するために上からの写真も必要になる。図13の左側の写真は、フィレット先端が少し盛り上がって見えているものの、これはんだ量が多いためなのか、あるいはフラックスの劣化でぬれ上がっていないのか判らない。しかし右側の写真では、フィレットのデンドライドやフラックス残渣やぬれ上がり状態から、フラックスの熱反応を推測することができるのである。
図13
量産現場のない国内では、再現実験すら実施することができない。私が出張で工場指導する場合でも、他社の工場で勝手にラインを使うと、『その間に発生した不良品やトラブルに対する保証』という問題が起こる。
出張担当者レベルでの限られた時間では対処できていないのが一般的で、同時に相談できる相手もおらず、逆にローカルの技術者には責任問題があるため、指示されたことしかできないものである。
ローカル工場の技術者相互間のレベルでは合意確認されていても、現場では品質の意味を十分に理解せず、そのつど現場の都合で作業していることが多く見られる。ライン監査をする場合は、まず最初に修正工程で修正内容をみて、それを簡単な確認・再現実験方法で現場に見せて理解させるという手順を踏む。これはスポーツや料理と同じで、理論やマニュアルのみを教えるのではうまくできないのであって、必ず練習が必要なのである。
以前であれば、簡単な実験をする場合はすぐに基板や部品が用意されたものである。現在は中国でも無駄な在庫や税金の関係ですぐにはできないものの、マイクロスコープを用いた動画の活用で、かなりの部分を補うことができる。
解析を外部に委託する場合は、これらの情報を基に仮説を立ててから、あらかじめ解析部分や内容を絞ったうえで依頼すべきである。情報不足のまま依頼すると、現象は判っても現場での改善方法までは出てこないので、もったいないことに解析のための解析で終わっているケースも多い。
技術の向上と共に不良原因も複合的な要因によって起こっているもので、短期的に改善できたように見えてもしばらくしてまた同じようなトラブルが起こりがちであるが、これは実施した改善内容(解析内容)が十分でなかったか、他の隠れた要因によるものである。
国内のマザー工場で基本的な量産技術やデータを蓄積していなければ、海外を含む外部へ実装を委託して市場で初めて問題が起きてしまってもその事態への備えがないことになる。部品や図面があれば製品ができる、というレベルの品質やコストのものづくりであればいうことはないのだが、そうではない。現状では多くの技術者が海外工場へ出張しているのである。
- 会社名
- 実装技術アドバイザー
- 所在地
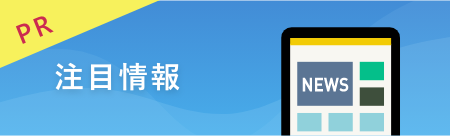
-
真空リフロー、N2リフロー、エアリフローのことなら、エイテックテクトロン(株)にお任せください。フラックスレス真空リフロー装置販売開始!エイテックテクトロン株式会社
-
独自の加工技術とノウハウで様々な材料にチャレンジ 〜色々なアイデアを生み出して研究者をサポート〜 ムソー工業株式会社 代表取締役 尾針 徹治 氏Gichoビジネスコミュニケーションズ株式会社
-
話題のGlass PKG実装技術の動向 〜先端電子部品への応用と 最新のCuダイレクトめっきGWCについて〜 Grand Joint Technology Ltd 大西 哲也(T. Onishi)Gichoビジネスコミュニケーションズ株式会社