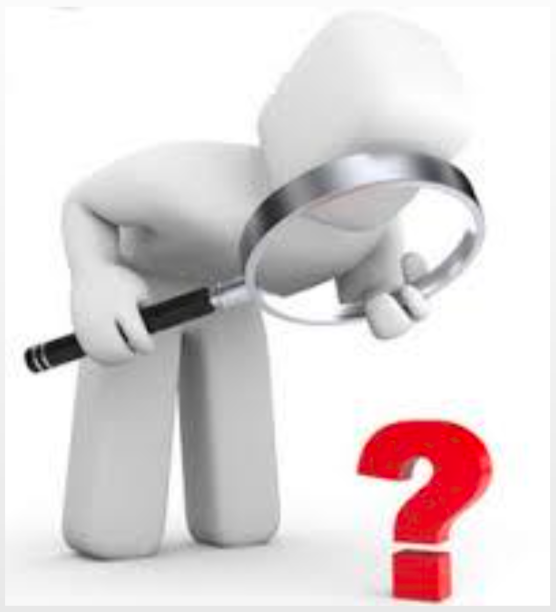
3. 「視点」は解釈
以上、あらゆる場面にを想定して「みる」について説明をしてきた。なぜあんなに細かい説明をしたかというと、われわれ人間は物事を正しく見ていないことのほうが多いからである。
自分の目に飛び込んできた映像を「そのまま見る」というのは、実は至難の技である。それほど人間というのは、ただ見るということが難しいのである。脳が発達しているからかもしれない。
つまり、人間は目の前に現れた出来事を「解釈」しながら「みている」のである。そしてその出来事は解釈によって判断が異なる(図2)。
頑固な人がいる。頑固、ということも、悪い言いかたをすれば「頭が固い」「融通が利かない」などの解釈が可能である。しかし逆の解釈の仕方をしてみてみると「我慢強い」「諦めない」「心が強い」などの判断も可能になる。
「気が弱い」「気が強い」、これらのことも同じである。人は多くの場合、今自分が遭遇している環境を変えようとする。今のその状況に満足していないからである。仕事で言えば不良が出ている、というその状況を変えようとすることは、おそらく私生活でも同じようなことがいえるであろう。
しかし周りを変えようとすることができるのは、非常に大きな力をもっていないと不可能である。お金も時間もかかるのである。解釈を変えることは、お金も時間もかけずに簡単に変えることができる。
不良を改善できていない工場では、不良を改善できていない工場のエンジニアは、この解釈を変えることがまずは大事である。「毎日、満員電車で通勤に2時間かかる」。これを変えるにはどうしたらいいか?
不良改善できていない工場のエンジニアは、図2で示した回答で言うところの上から二つ目までしか出てこない。つまり、「近くに引っ越す」とか、「通勤時間中に本を読む」とか、かかっている時間を短くする方法をとるか、かかっている時間を有効活用するための方法をとるか、そのいずれかの案しか出てこない。
これを工場内の具体的な事例に置き換えて話をすると、たとえばはんだの温度が250℃±5℃の範囲で調整が、管理条件上を可能であったとする。すると、改善できないエンジニアは、245?255℃の範囲で改善することが可能かどうか?を検証しだすのである。もともとの管理条件が不適切であるとは可能性すら考えないのである。
なので先の事例でいえば、「会社を辞める」という発想は出てこない。入口か間違っているのである。私の講義ではよくお話をする話なのであるが、入口を間違えた場合、出口にはたどり着かない。特にエンジニアリングはそうなのである。
改善を行うときは、広い範囲に視野をもっていただきたい。はんだ付け条件の改善を行う場合、私であればはんだの温度の検証はそのはんだの融点から行う。Sn3.0Ag0.5Cuの鉛フリーはんだであれば、融点は約220℃なので検証の最下限値は220℃に設定する。
「それでは…はんだがつかないのではないですか?」
まったくその通りである。だがここに設定の最下限値をもってくることが重要なのである。はんだの融点以下の設定では、はんだが溶融しないので、「その設定値は間違っている」ということがいえるはずである。
では、はんだが溶けた後、+何℃からはんだ付けは可能になるのであろうか? このようなことを検証するのが真のエンジニアリングであると私は思う。このように、ありとあらゆる事が検証済みであるからこそ、ありとあらゆる事を調整することができている、といえるのではないであろうか。
このような発想が頭の中からすぐに出てくるように、あらゆる出来事に関して解釈の仕方を何通りももつようにしておこう。それには普段から、そのような考えをもっていることが重要である。つまり日常生活においても、これまでの解釈の仕方を変えてみる、解釈を何通りか考えてみる、ということを行ってみていただきたい。必ず改善活動に役に立つ。
図2 「視点」と解釈
4. 比較して「みる」視点
次に、私が実際に指導している実装工場で取り入れてもらった事例を紹介する。
工場内には必ず「検査工程」というものが存在する。そこで皆さんにお訊ねしたい。
「朝の朝礼がある場合、検査工程の作業者も全員朝礼に出ていますか?」「朝礼の後、すぐに検査を開始しますか?」
この質問をセミナーなどで行ってみたところ、かなり多くの会社のかたが「YES」とお答えになられた。なので別に間違っているということではないのである。では何をコンサルティング先の工場で採用してもらったか?
それは、
①検査工程の作業者は朝礼に出なくてよい、ということ。
その代わり、
②「朝の目のトレーニング」を行うこと。
この二つである。
もちろん、朝の朝礼には検査工程の作業リーダーだけは出席してもらって、そこでの情報は作業者に展開してもらうようにする。
私が言いたいのは、検査工程の作業者のかたがたは、朝のまだ眠い時間に、聞いてもいない朝礼なんかに出席してもらうよりも、まだ寝ぼけている可能性がある朝であるからこそ「目のトレーニング」をしてもらいたいということである。
とはいえ、朝からはんだ接合部を「標準見本品」などを用いて目のトレーニングをしてくださいと言ったところでほとんどの作業者が「見ているふり」をするであろう。そうではなく、楽しみながら目のトレーニングができれば一石二鳥である。そこで考案したのが、間違い探しの採用である(図3、図4)。飽きてしまうと困るので、曜日によってやる事は変更すれば良い。
間違い探しだけではなく、『ウォーリーを探せ』など、趣向を凝らして作業者に飽きさせない工夫が必要である。
さて、皆さんはすべて見つけることができたであろうか。思ったよりも多く間違いがあったことがわかったことと思う。このように検査員かたがたは、朝の一番から、またはお昼ご飯を食べてすぐ、製品において良否の判定をしなければならない。なので不良を見つける目を養わなければならないのである。
その「不良見つける目」は、いきなり開花するものではない。日々の努力の積み重ねで養われていくものなのである。
このように、遊び半分かもしれないが、検査員のかたがたには、朝の朝礼に行ってていただくよりも「不良見つける目」を発揮していただく準備運動をしていただいたほうが検査精度の観点からいってもよいといえるであろう。
図3 比較してみる視点(良品と不良品の差異を明確にする)
図4 図3の答え
- 会社名
- (一社)実装技術信頼性審査協会、STCソルダリングテクノロジセンター
- 所在地
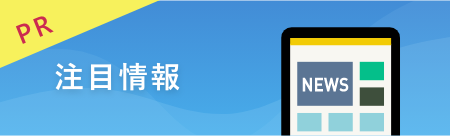
-
真空リフロー、N2リフロー、エアリフローのことなら、エイテックテクトロン(株)にお任せください。フラックスレス真空リフロー装置販売開始!エイテックテクトロン株式会社
-
独自の加工技術とノウハウで様々な材料にチャレンジ 〜色々なアイデアを生み出して研究者をサポート〜 ムソー工業株式会社 代表取締役 尾針 徹治 氏Gichoビジネスコミュニケーションズ株式会社
-
話題のGlass PKG実装技術の動向 〜先端電子部品への応用と 最新のCuダイレクトめっきGWCについて〜 Grand Joint Technology Ltd 大西 哲也(T. Onishi)Gichoビジネスコミュニケーションズ株式会社