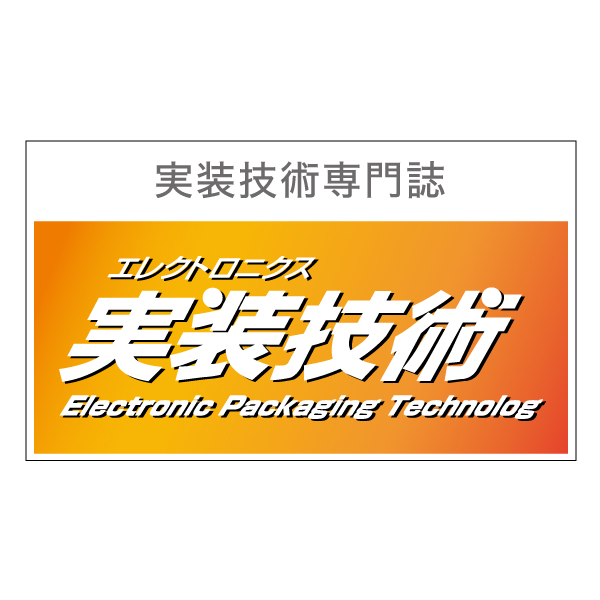
③アンダーフィル工程の前処理
ここでは大気圧プラズマが利用されている一例としてアンダーフィル前の表面処理を紹介する。
基板に用いられる有機素材と半導体デバイスの熱膨張係数が異なる。そのため、温度変化による応力が、特にはんだボールを介した接合部で大きくなる。対策として、樹脂材料をアンダーフィル材として封止して、応力を部品単位全体に分散させることが多い。この封止材の剥離防止の目的からプラズマによる表面改質が活用されている。まず、接合前に基板の表面に処理を行うノーフローアンダーフィル工程での活用例がある。またリフロー後、キャピラリーアンダーフィルの直前に、デバイスの縁を上からなぞるような形で(つまり、アンダーフィル剤をまさに塗布するのと同じような形で)プラズマを照射する場合もある。後者の場合ではプラズマははんだボール間のわずかな間隙に入っていき、その過程でアンダーフィル材の密着相手となる上下の基材および接合後のはんだボールといった表面を改質することができる。
このように、パッケージレベル、ボードレベルのいずれにおいても、アンダーフィル材の迅速で広範な濡れ広がりが実現し、気泡の抱き込みが抑制され、接合維持に繋がっている。
④大気圧プラズマによる酸化被膜除去
大気圧プラズマによってインラインで酸化被膜を除去することで接合信頼性を向上する事例もある。この場合、酸化被膜を除去するには、水素と窒素の混合ガスをイオン化ガスとしとして用いることで、大気圧プラズマによる強力な水素還元プラズマの作用を活用する。
酸化被膜を除去するのには様々な目的があるが、はんだの濡れ性向上がまず挙げられる。ダイボンディング前、あるいは樹脂封止の前洗浄として使用されている事例もある(図4)。
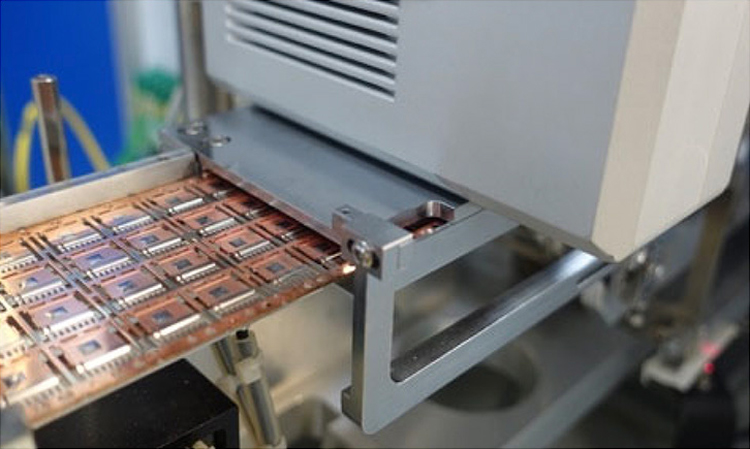
図4 大気圧プラズマ インライン処理例 (Plasmatreat提供)
ここで、大気圧プラズマの酸化還元処理によってはんだ濡れ性試験の結果を掲載する(図5、6)。ここでは、試験片(銅板)を溶融はんだにディッピングし、はんだの濡れ上がりに要する時間(ゼロクロスタイム)と、最大濡れ力を測定している。
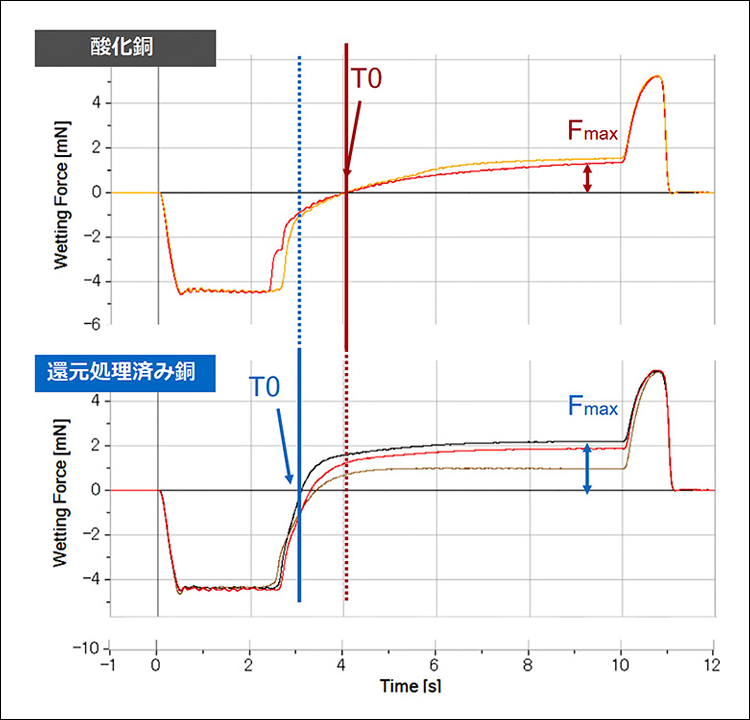
図5 はんだ濡れ性試験結果① (Plasmatreat提供)
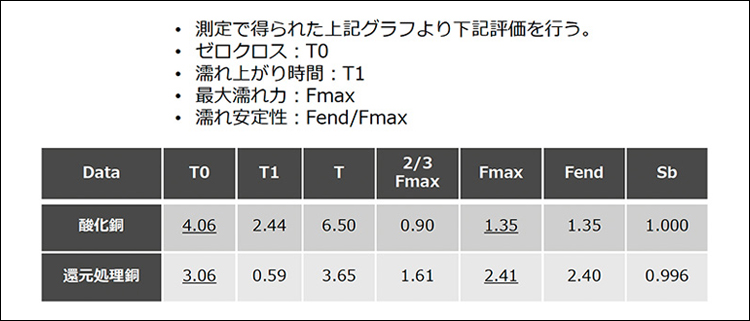
図6 はんだ濡れ性試験結果② (Plasmatreat提供)
大気圧プラズマ酸化還元を行った試験片において、濡れ上がりの時間が短くなり、最大濡れ力も増加していることが確認できる。
はんだのボイド発生原因は複数あるとされているが、接合対象となる金属表面への被覆(濡れ)がボイドの抑制に繋がるとされる1)。そこでフラックスが、はんだの付け阻害因子である酸化膜を除去することを目的に用いられる。他方、ボイドが発生する主な原因の一つとして、はんだに含まれているフラックスがガス化して内部で留まることであるとされている2)ため、フラックスを使わない、あるいはフラックスの使用量を最小限に抑えつつ、相手金属表面がはんだで被覆される状態が望ましい。
また大気圧プラズマによる酸化還元は、活性剤を添加するといった、はんだ側の変更を必要としないため、エレクトロケミカルマイグレーション等の懸念や、材料のコストアップを避けられることも利点といえる。
⑤高温動作環境やシンタリングプロセスへの対応
さらに、その大気圧プラズマを活用して大気圧下でプラズマCVDにて表面に機能性ナノコーティングを施す技術(図7)の重要度が増している分野がパワーエレクトロニクスである。
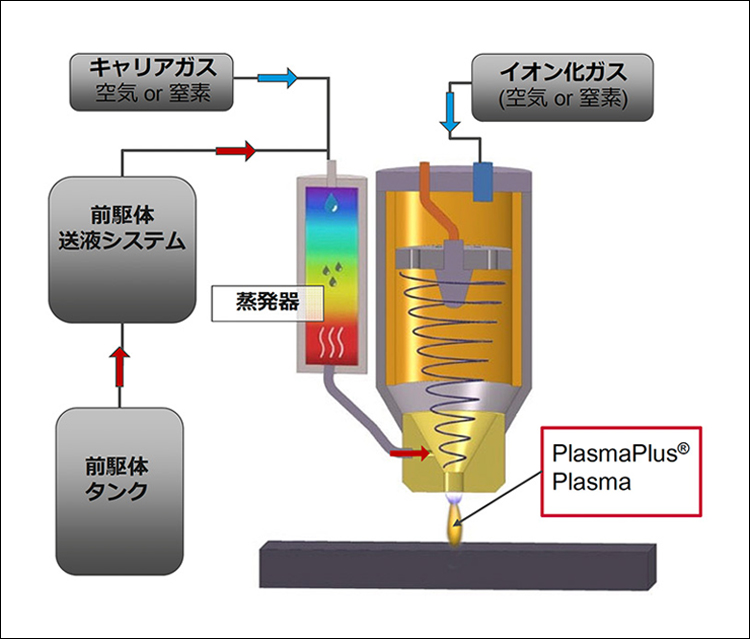
図7 PlasmaPlusプラズマコーティング装置概要(Plasmatreat提供)
パワーデバイスの代表的なモジュール構造として、半導体チップがアタッチされた絶縁基板をさらに金属放熱板上に固着させ、チップをワイヤボンディングなどで電気的に結線したあとは、樹脂封止にて接合保護する形がある。
ここで、前述の大気圧プラズマによる酸化被膜除去処理に加えて、大気圧プラズマを活用したプラズマナノコーティングで樹脂封止材の初期密着強度および長期使用環境下における接合確保が可能となる。追加のコーティングの役割は、封止に使われる有機材料と導電用の金属材料との熱膨張係数の差による応力を吸収・分散させられる強固な結合層を作ることだが、大気圧プラズマCVDを活用することで膜形成を瞬時に成立させることができるのが最大のメリットの一つだろう。乾燥工程を必要としないため、乾燥に必要な所用時間および追加エネルギーを省略しつつ、次工程である封止プロセスへの工程の直結が可能となる。
特に昨今では、電子やホールが価電子帯から伝導体へ遷移するために必要なエネルギーがより大きい、SiCなどのワイドギャップ半導体に注目が集まっている。ますますの小型化と大電力化により放熱密度が上昇していく動向のパワーエレクトロニクスデバイスでは、はんだ溶融温度以上の動作環境を想定する必要が出てくる。そのためアセンブリ実装形態においても両面直接冷却などの熱応力緩和対策も取られている。他方、半導体デバイスの耐熱性と放熱性の両方の向上のために、例えばダイアタッチとして銀や銅ペーストを導入することが検討されており3)、そもそも製造プロセスにおいてパッケージがさらされる熱負荷自体が非常に大きなものとなる。そのため熱負荷自体を軽減する措置を最適化すると同時に、やはり高信頼でより高い接合温度を確保することが重要となっている。
- 会社名
- 日本プラズマトリート(株)
- 所在地
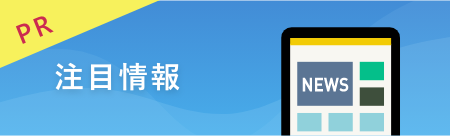
-
真空リフロー、N2リフロー、エアリフローのことなら、エイテックテクトロン(株)にお任せください。フラックスレス真空リフロー装置販売開始!エイテックテクトロン株式会社
-
独自の加工技術とノウハウで様々な材料にチャレンジ 〜色々なアイデアを生み出して研究者をサポート〜 ムソー工業株式会社 代表取締役 尾針 徹治 氏Gichoビジネスコミュニケーションズ株式会社
-
話題のGlass PKG実装技術の動向 〜先端電子部品への応用と 最新のCuダイレクトめっきGWCについて〜 Grand Joint Technology Ltd 大西 哲也(T. Onishi)Gichoビジネスコミュニケーションズ株式会社