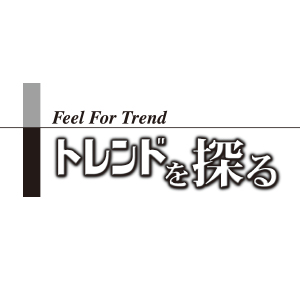
4.モビリティー
本節では、近年の自動車のキーワードであるCASE(Connected、Autonomous、Shared、Electric)をベースに、 自動車の自動運転化、コネクティッド化、電動化について解説した。電動化では、自動車以外に鉄道や航空機の電動化動向についても触れている。
最後に、エンジンルーム内・外に搭載される電子機器ユニットの動向についても解説した。
自動運転化では、特に自動運転に向けた制御において、車両内の認知判断のみでなくダイナミックマップ生成など、車両外システムにも、人工知能(AI)技術が重要な位置づけとなることに触れ、それを用いた車両統合制御ECUおよび、それらとステアリング、ブレーキ、サスペンションなどのアクチュエータとの関連についても解説している。
コネクティッド化では、図10に示すような自動車を取り巻く通信環境全体を概観した後、ETCなどで実用化されているDSRC、ADAS/自動運転に向けたセルラV2Xについて詳述しており、さらに今後の5G通信への期待についても解説している。
図10 自動車で使用されている主な通信
特に車外無線通信の例として、TCU(テレマティックスコントロールユニット)の実装形態の変遷と最新の実装例を示し、搭載部品の分析も行った。
電動化では、パワーデバイス市場動向の解説、自動車の電動化につき、電動車の構成と市場動向、将来に向け、低損失/小型化を可能とするSiCデバイスへの期待につき解説した。
また図11に示すような、パワーデバイス・インバータ構造の高放熱化トレンドを示している。
図11 パワーデバイス・インバータ構造の高放熱化トレンド
さらに電鉄において実用化が進んでいるSiCパワーモジュールの動向とその効果についても解説した。
また、今後適用が拡大すると予想される航空機の電動化システム、ロードマップならびにその課題についても解説している。
最後に、エンジンルーム内、外に搭載される電子機器ユニット(ECU)それぞれにつき、製品仕様、実装仕様、半導体・電子部品・プリント配線板への要求動向という視点でまとめた。
5.新市場・新材料・新技術
2017年度版に引き続きサーマルマネジメントについて解説している。
今回は17年度版で記述できなかった具体的な設計の考え方について触れた。
まずは熱伝導設計では高熱伝導材料とともに、接触熱抵抗の論理的な算出方法を通して熱伝導材料(TIM)の選定について論じた。
具体的な製品については、車載用を中心にパワーデバイス(図12)について説明し、モバイル機器ではスマートフォンのサーマルマネジメントについて説明している。
図12 インバータパワーデバイスの放熱構造
新市場としてマイクロLEDを取り上げた。
2014年にApple社がマイクロLEDのベンチャー企業であるLuxVue社を買収したことからOLEDに続く次世代ディスプレイとして注目されている。
図13にマイクロLED関連特許の出願動向を示す。
図13 日本におけるマイクロLED関連特許の出願動向
製造方法に関する出願が近年増加傾向であることがわかる。
特徴や課題である実装方法、実装スピードについて解説した。
4KディスプレイにはLED素子としても2,400万個の実装が必要となり、実装スピードはマイクロLEDの汎用化の最大の課題となる。
また、新技術として次世代通信5Gについて解説しました。
実証実験の内容と課題解決に対する新技術として、MIMO技術、メタマテリアル技術について概説し、材料としては低損失に必要な低誘電率、低誘電損失の材料の開発動向について論じました。
低損失通信の実現には、5Gの領域で低誘電特性を示す材料が必要となっている。
これまで多く活用されたガラエポ樹脂から、LCP (液晶ポリマー)、ガラス、フッ素樹脂などの活用が検討、開発されている。
3. 電子デバイスパッケージ
本章では、IoTの普及とともに多様化が進む半導体パッケージの注目される動向に関して記述した。
従来、小型パッケージ用途に用いられてきたウエハレベルパッケージは、FO-WLP構造(図14)を取ることによりスマートフォン向け多端子パッケージへと適用範囲を広げてきている。
図14 FO-WLPの製造プロセスの事例
さらに外形をウエハ形態からパネル形態に変えたパネルレベルパッケージによって低コスト化が試みられている。
現在各種方式が提案されているが、本章ではそれらの特徴や課題解決の手法を記載した。
また異種混載・高密度実装技術としてPoPとSiPを取り上げ、現在開発が進められている5G向けSiP技術に関しても記述している。
またレガシー技術と考えられていたワイヤーボンディング技術に関しても、そのユニークな形状制御技術(図15)を駆使して、RF部品等の形成が試みられている状況を紹介した。
図15 ボンディングワイヤーで形成したRF部品
出典:新川
4. 電子部品
本章では、実装技術に影響を与える「L:インダクタ」「C:コンデンサ」「R:抵抗器」「EMC対策部品」「センサ」「コネクタ」を前版に引き続き取り上げて技術動向を解説している。
また、CASEの進展で大きく注目される車載向け電子部品の動向について解説を充実させ、「入出力デバイス」を追加して車載向けの技術動向を中心に記述している。
「LCR部品」と「EMC対策部品」では、実装技術動向のひとつの指針となるチップ部品のサイズトレンドを提示している。
本誌10月号に掲載された「電子部品技術ロードマップの概要」でも紹介している。チップ部品のサイズ比較を図16に示す。
図16 チップ部品のサイズ比較
同図中に示す0201サイズは小型化要求の強い製品から採用が増えていくと考えられる次世代チップサイズ、01005サイズは開発品として提案されているチップサイズとなる。
「センサ」ではADASや自動運転技術に必須となるセンサを紹介し、MEMSセンサを中心に技術解説をしている。
現在自動車向けで使われる主なMEMSセンサを図17に示す。
図17 自動車向けで使われる主なMEMSセンサ
「コネクタ」では車載用ハーネス・コネクタの概要とアンケート結果からの将来動向を、そして搭載数が増加する車載用カメラコネクタを取り上げて、技術動向を解説している。
追加した「入出力デバイス」では、DMSや乗員検知などで求められる「ToFデバイス」、また「タッチパネル」と「車載HMI」を取り上げて技術動向を解説している。
5. プリント配線板
本章で解説したプリント配線板技術は、日本電子回路工業会(JPCA)が2019年6月に発行したプリント配線板技術ロードマップから抜粋したもので、詳細はそちらを参照していただきたい。
今般のロードマップの重要なメッセージは、従来からのプリント配線板製造技術での微細化追求が終焉を迎えたことと、さらなる微細化がウエハレベル製造プロセスで進展することを紹介したことである。
またプリント配線板製造技術の方向性として微細化の追求(図18)と反して高付加価値化の追求としてのストレッチャブル、コンフォーマブル、およびテキスタイル回路基板技術についても紹介した。
図18 プリント配線板の微細化動向
我が国プリント配線板産業は10年前まで世界第1位の市場占有率を保有し、技術リーダーの役割を果たしてきた。
約10年前のリーマン・ショックから生産金額、生産量ともに減少し続けている。
しかしプリント配線板の応用範囲は前述の通り拡大しており、加えて我が国の技術的リーダーシップへの期待は依然として高いものがある。
世界の期待に応えることも我が国プリント配線板業界の重要な役割のひとつである。
図19にガラスサブストレートの技術ロードマップを示す。
図19 ガラスサブストレート技術ロードマップ
コア層材料のガラスは、熱膨張係数 (CTE: Coefficient Thermal Expansion) が3.2 ppm/K‐3.8 ppm/KとSi に近似しているボロシリケート(Borosilicate) ガラスを現在入手可能な材料として最適としている。
しかし、追加コストがなければCTE は3.0 ppm/K に近づくことが望まれる。10GHz時の比誘電率(Dκ)は、ボロシリケートガラスの6.0 としたが、伝送損失を小さくするには、少なくてもFR-4 と同等の4.8、あるいは4.0 に近づけることが望まる。
同じく10GHz時の誘電正接(Df)は0.002としたが、機能集積基板の標的市場のRF SiP の対象周波数の30~140GHzで伝送損失を抑えるためには0.002以下になることが求められる。
コア層厚さは、ウエハプロセスとパネルプロセスともに材料ハンドリングの視点から300μmとした。
しかし、ループインダクタンス(Loop Inductance)削減のためには、前述のプロセスでも100μm厚さを取り扱う必要がある。
また、ビア加工費削減と連続大量生産による低コスト化のため、ロールツーロール生産に対応できる100μm以下が2020年以降に登場すると予測した。
なお、ビア径はCO2レーザーで穴あけ可能な数値を入れている。
300μm厚さのコア層での最小ビア径は75μm、100μm厚さのコア層でのビア径は30μmとした。
これらのデザインルールは、現在のビルドアップ構造サブストレートのビルドアップ層ビア径と近似しているが、ビルドアップ層のCTE α1 がX-Y-Z 方向で20ppm/K程度に対し、ガラスコア層は3.2ppm/K~3.8ppm/Kと寸法安定性が高いため、実装密度を妨げるビアランド(Via Lands)を設ける必要がない。
このため、ビルドアップ構造サブストレートよりも高密度配線が可能になる。
本ロードマップでは有機樹脂サブストレートに関しても記述している。
6. 実装設備
本章でははじめに実装設備業界の近年の概況、次に生産性の現状と動向に触れたあと、本章の特徴である全世界の設備ユーザーへのアンケート結果を元に、設備各モデルにおける市場の要求順位と動向について紹介している。
モデルとは具体的には、印刷機、マウンタ、リフロー、検査機、ベアチップ/フリップチップボンダである。
これに加え、設備で共通に関係する接合材料と封止材料についてもアンケートを実施した。
実装設備で基本となる生産性は、毎年のように向上し続けているが、たとえば現在マウンタで達成している最高速の50,000cph(1時間あたり50,000点装着)は、構造的に見て限界に近いので、今後の伸びは緩やかになると予想している。
そのかわり、搭載すべき部品が超小型化し、電子回路が高密度化する傾向は続いているので、印刷や実装・検査の精度向上とその維持の自動化要求は継続して高まっている。
アンケート結果の例として図20にマウンタに対する要求順位と経過を示すが、どの設備においても本要求は上位になった。
図20 マウンタに対する要求順位と経過(抜粋)
末尾のトピックスコーナーでは、今春完成したばかりの設備間通信規格ELS:イーエルエス(Equipment Link Standards)について取り上げている(図21)。
図21 ELSの概要
この規格は日本の実装設備メーカーが中心となって、国際規格化出来た事例である。
近年需要が高まっている変種変量生産への高速対応や、集中制御によるライン稼働効率化、またPCBの情報をPCBの生産に1対1で同期して受け渡す「情物一致」という要求に対応できることが期待される。
7. 最後に
超スマート社会Society 5.0実現への貢献のため、電子実装技術の視点で、今重視すべき課題が何で、どのような解決策があるか、どのような方向に進むのかを描き、投げかける必要がある。
半導体の方向性は、More Mooreが依然として進み、極限まで微細化をめざす一方で、異種デバイスを融合する新基軸デバイスのMore than Mooreも進化をしている。
この状況はしばらく維持されるものと予想している。
この中で電子実装を取り巻く各種ロードマップ活動の見直しが進み、微細化が終焉した先の新たな展開・今後の方向性の提示も必要になる。
そうした中でロードマップ活動を継続し、今後もロードマップを発刊することは我々に課せられた使命と認識している。
引き続き時代の変化に対応した、ステークホルダーに価値を感じていただけるロードマップづくりに取組んでいきたいと考えている。
最後に、実装技術ロードマップは、最前線で活躍する実装技術専門家の予測やワールドワイドな市場・技術動向調査を基に、時代の変化への対応を展開した内容となっている。
実装技術業界のみならず関連する材料・製造装置業界に対して、研究開発すべき技術のガイドブックとしてご活用いただき、新しい市場やビジネスモデルの創出の一助になればと考える。
<参考URL>
JEITA ホームページでの「2019年度版 実装技術ロードマップ」申し込み先
https://www.jeita.or.jp/cgi-bin/public/detail.cgi?id=740&cateid=1
- 会社名
- Gichoビジネスコミュニケーションズ株式会社
- 所在地
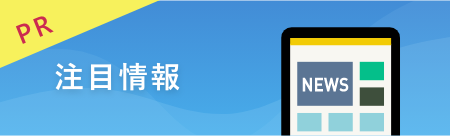
-
真空リフロー、N2リフロー、エアリフローのことなら、エイテックテクトロン(株)にお任せください。フラックスレス真空リフロー装置販売開始!エイテックテクトロン株式会社
-
独自の加工技術とノウハウで様々な材料にチャレンジ 〜色々なアイデアを生み出して研究者をサポート〜 ムソー工業株式会社 代表取締役 尾針 徹治 氏Gichoビジネスコミュニケーションズ株式会社
-
話題のGlass PKG実装技術の動向 〜先端電子部品への応用と 最新のCuダイレクトめっきGWCについて〜 Grand Joint Technology Ltd 大西 哲也(T. Onishi)Gichoビジネスコミュニケーションズ株式会社