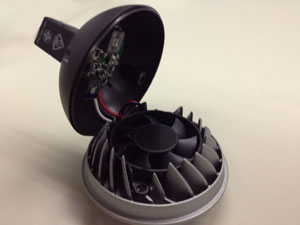
1. 長寿命設計と開発期間の短縮
電子機器は、非常な勢いで軽量小型化を目指してきている。
その中で、過去、中心を占めていたセラミックパッケージは、その重量とパターン密度が低いことから、パターン精度が高く軽量かつ安価なプラスチックパッケージにその主役を奪われて、はや20年近くが過ぎている。
一方、プラスチックパッケージの電子機器への登場については、非常に多くの信頼性課題が克服されねばならなかった。
プラスチックの欠点は、
①熱に弱い、②熱を伝えにくい、
③耐水性に問題がある、
④耐候性で特にUV耐性の低い物が多い、
⑤接着信頼性に欠ける、
⑥膨張係数が高く無機材料との接合信頼性に劣る、
⑦廃棄問題、
などが挙げられる。
プラスチックは、熱を逃がさない、すなわち熱伝導率が低いことが電子機器に採用するにあたっての欠点とされている。エンプラ、スーパーエンプラと耐熱性の高いプラスチックの開発は目覚ましいが、熱伝導という観点からの開発はあまり進んでいないのが実情である。
本稿では、これらの熱対策につき、最近非常に注目を集めているLED照明の観点から記述する。
2. LEDの熱との戦い
現在、LEDも照度が800lm以上の明るい照明が主流を占めるようになってきた。これは、100lm/W以上の高い発光効率の高輝度パワーLEDの出現などを実現させた、多くの技術者の血の出るような努力の賜物である。
その内容は、LED素子自体の徹底した開発、周辺の材料の最適な選択と改良、反射を最大限利用した光の最適な取り出し方など多くの課題克服によるものである。その中で、大きな問題とされているLEDの熱に対する状況を見てみよう。
たとえば、1000lmの明るさをもつ単体のLED照明を考えてみる。この場合、発光効率100lm/Wとして消費電力は10Wになる。ごぞんじの通り、LEDの消費電力の約80%が熱に変わるから、8Wの熱が発生することになる。たかが8Wだが、LED自体の大きさがせいぜい1cm□程度だから、この面積で8Wの熱を受けていることになるのだ。
単純に、こたつで考えてみると、普通500W程度のヒータでの暖房が多いが、その放熱面積は30cm□程度であり、面積は900cm2となるから、単位面積当たりの発熱は0.55W程度である。単純計算すると約15倍になる。いかにLEDが、局部熱が発生しているか良く分かる事例である。そして、普通ジャンクション温度は125℃である。LEDにおける発熱は、ヒートスプレッド(熱を広げる材料)なしでは、5分もたたずに160℃を超えてしまう。LEDが高い温度になればその電気抵抗が上がるから、さらに発熱することによる昇温による熱暴走が生じる危険性を伴っている。たとえば銅の抵抗率は0℃と100℃で比較した場合約1.5倍まで抵抗は上昇する。
だから速やかに、LEDから熱を逃がす必要がある。
LED素子の表面は普通エポキシ樹脂或いはシリコーン樹脂で封止されている。特に主流を占めるエポキシ樹脂での封止では、その耐熱温度が低いことから黄変することが報告されており、耐熱改質を現在も継続して検討されている。一般エポキシ樹脂の場合、120℃でもわずかか500時間程度連続でその程度の温度がかかれば、その透過率は80%以下になる事例が多く報告されている。
LEDの寿命は照度が初期の70%を切った時点までとされるから、高輝度で連続照明した場合、70%以下の照度の保証は40,000時間が本当に大丈夫か懸念されるのである。
とにかく、LEDの熱をすばやく移動させることが大切であり、電子機器のもっとも重要な信頼性を確立させる大きな因子となっているのがLEDからの放熱技術である。
今年7月にはLEDにもPSEマークが必要とされるなかで、安全面、信頼面からも放熱を抜きにしてLED照明の製造を行うことは非常に危険であることは周知の事実である。
LED自体の熱を逃がす一番簡単な熱回路は、電流を流す金属導通回路である。そのため、熱伝導の高い銅などを使用したリードフレームを使用したり、回路基板も熱を逃がすサーマルビアを設けてすみやかに基板裏側に伝熱する方式が一般的に採択されている。回路基板自体も、熱伝導率の高いセラミック基板、さらには窒化アルミ基板などが使用され、裏面はアルミなどの金属を貼り付けているものが高輝度パワーLEDでは主体となる。LEDから基板への熱移動はリードフレームの熱を回路基板に移せばよい。回路基板の裏面への熱移動はスルーホールなどを通してすみやかにその下にあるヒートシンク(放熱板)にせねばならない。
3. 熱を伝えるということ
熱を伝える方法は伝導、対流、輻射である。
熱伝導は、熱エネルギーによる分子振動の伝達とされる。対流は、熱を与えられた結果、気体及び液体における熱を伴う移動が生じるものである。輻射は、熱が電磁波転換され、放射されるものである。
さて、LEDにおける熱を伝える実際のメカニズムとは何か考えてみる。
各式からみれば熱を早く伝える要素は
①温度差があること
②それ自体の熱伝導率が高いこと
③熱伝導率が小さい材料では、熱が伝わる距離を短くさせること
などが各式から一目瞭然である。
4. LEDでの伝熱について
一番分りやすい事例としてLED搭載の基板の熱をヒートシンクに熱移動させるメカニズムについて考えてみる。
まず基板とヒートシンクを直接ねじなどで貼り付けた場合、どうしても反りなどにより空気の隙間層が生じる。空気の熱伝導率は0.02W/m・Kと非常に小さいため、この隙間層があるだけで、完全断熱に近い状態を呈してしまう。普通50φ程度の大きさを想定した場合、反りなどによる隙間は平均200μ程度と考えられるから、薄い断熱層ができていると考えてもよい。
それで、その隙間を埋めるためにサーマルグリスなどを塗布することが一般的である。問題は、サーマルグリスが液状であることで、高温になった場合、サーマルグリスの粘度は下がり流れやすくなる一方、上下にあるヒートシンクと回路基板の膨張係数が異なることから、温度差による応力がサーマルグリスにかかることでサーマルグリスが外部に追い出されるという点である(ポンピングアウト現象)。
以上から、一定の安定した品質を確保するにあたり、単なるねじ締め及びサーマルグリスの塗布については、熱安定性で多少の危険性が生じる。もちろん、各社様々な改善がなされており、個別製品では確立された新規技術により課題はかなり改善されてきている。
主流となっているのは放熱シートである。このシートは耐熱についてはシリコーン樹脂が多用されている。シートを最適な形状に打ち抜きヒートシンクと基板の間に挟み込みネジ留めなどで固定する。普通絶縁性も放熱シートで保証される。しかしその熱伝導率は絶縁性も必要なので、1~2W/m・K程度が主流である。
熱抵抗を考えた場合、放熱シートの厚みを薄くすることが良いが、作業が難しく、すぐしわなどが生じたり、うねりなどによる隙間ができたりするので0.5mm以上放熱シートが主流となっている。それと、放熱シート自体がヒートシンク及び回路基板に密着しないと熱を伝えにくくなる。そのため、粘着力に高い(別の言い方をするとすごく硬度の低い)放熱シートが必要になる。
硬度が低い放熱シートは普通熱伝導フィラーの量も少し低減されるので、熱伝導率自体はあまり期待できない。
しかし、ねじ締めなどで抑え込む時の圧力によりその硬度の低さで薄くなることとその密着力で、熱抵抗は低減できる。やはり、一番熱抵抗を少なくする手段でポンピングアウトなどがない形式なのは、熱伝導接着剤による貼り合わせになるだろう。
この場合、各被着体の凹凸を埋め込みながら最少厚みで接合できるため、その厚みは100μ程度で済み、選択する樹脂により様々な物性を調整することが可能である。
一方、接着したものは、剥離しづらいためリペアできない、樹脂硬化に対して加熱が必要である、また塗布状態により品質のばらつきが生じるなどの問題点を有している。
現在、筆者が提案している方法は、ヒートシンクか回路基板の熱移動表面にあらかじめ超柔軟性熱伝導樹脂を塗布硬化させる方法である。この方式だと、塗布された場所の凹凸を埋め込み相手方にはその柔軟な樹脂硬度により最少厚みで相手方に密着させることが可能である。大きさ及び貼り合わせ材料の反りを想定した最少厚みを塗布してねじ締めなどで固定すれば、最少厚みで密着出来、放熱シートにおける打ち抜き(切断)、貼り合わせなどの手間が省けるメリットがある。
- 会社名
- (株)ワイドワ?ク / 薩摩総研(株)
- 所在地
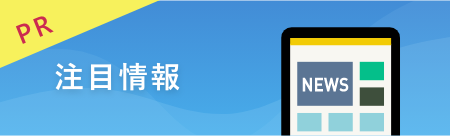
-
真空リフロー、N2リフロー、エアリフローのことなら、エイテックテクトロン(株)にお任せください。フラックスレス真空リフロー装置販売開始!エイテックテクトロン株式会社
-
独自の加工技術とノウハウで様々な材料にチャレンジ 〜色々なアイデアを生み出して研究者をサポート〜 ムソー工業株式会社 代表取締役 尾針 徹治 氏Gichoビジネスコミュニケーションズ株式会社
-
話題のGlass PKG実装技術の動向 〜先端電子部品への応用と 最新のCuダイレクトめっきGWCについて〜 Grand Joint Technology Ltd 大西 哲也(T. Onishi)Gichoビジネスコミュニケーションズ株式会社