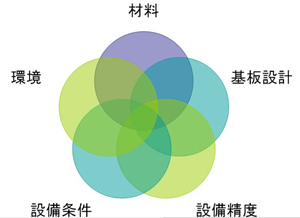
2011年3月
1年前、東日本大震災によって、当社(福島県・いわき事業所)も建屋の損害と水道の断水、加えて福島第一原子力発電所の事故による放射能の影響など、未曽有の体験をした。その際に皆様からたくさんの暖かいご支援や励ましのお言葉を賜り、本当にありがとうございました。こころより感謝いたします。
当社も震災発生の2週間後には生産を開始したが、取り引きのある部品メーカーにおいて金型が津波で流され、また設備損害で製造できないことなどがあり、部品調達に苦労した。しかし、その部品メーカーの皆様にも、早急かつ迅速な対応をしていただき、お客様には大きな御迷惑をお掛けすることなく対応することができた。誠にありがとうございました。
震災後、さらにタイで洪水問題が発生するなど、2011年は激動の年となった。
図1 不良対策の基本的な流れ
図2 不良を生み出す5つの要因
はじめに
前回(2011年4月号)は、『製造現場での不具合の解析は、不良の事象を良く見ることと、日頃から良品の状態を見ておくことが重要である』と書いた。今回はその続編として、不具合対策の流れを説明する。
図1は、基本的な不良対策の流れであるが、リフロー実装不具合対策は、このようなシンプルな流れにはならない。それはなぜか?
答えは、要因が複雑に絡み合い、そこから『これだ』という断定するまでの検証が非常に難しいからである。図2に示すように、5つの要因が関係しながら不良品が作り出されるのである。
不具合品を対策するまでの流れとスキル
不具合品を対策し、不良率を低減させるためには、図3の流れを作ることが必要である。
図3 不良を低減させるための流れ
流れとしては理解できるとは思うが、これを一つ一つ行うことは簡単ではない。そこが、不良対策の難しいところである。
以下に、流れの中で重要な、前半の4つの仕事のポイントを説明する。ここまでの仕事ができれば、対策は見えてくる。
①不良事象……観る。ただし、観る人のスキルに2つの要素が必要である。
1つ目は、『関心』である。関心がないと日頃から情報を取りに行かないので、情報不足となる。
2つ目は、『興味』である。興味がなければ勉強もしない、つまり知識が身に付かないのである。
②事実の把握……3つの要素が必要である。
1つ目は、『思想』である。原理原則に基づき、段階的に事実を並べていくことである。
2つ目は、『価値観』である。常に自分自身に合否の判断基準をもつことで、裏腹の事実が見える。
3つ目は、『素直さ』である。事実の把握は5W 1Hで把握するべきで、先入観は不要である。
③仮説立て……3つの要素が必要である。
1つ目は、『思想』である。説と説の関連付けを頭の中で整理しておくことが大切である。
2つ目は、『経験』である。わざと不良品を作ってみること。これが技術の蓄積となる。
3つ目は、『疑問を自答する』ことである。そのためには、上の経験から、ものさしを準備しておくことである。仮説を立てられるようになることは、特に失敗を恐れず日頃から行動することで養われる。
④仮説の検証……2つの要素が必要である。
1つ目は、『観察』である。仮説を実行した時の成り行きを時系列で観察していくことで原因がわかる。
2つ目は、『分析』です。原因は複合要因が大半なので、マトリックスを組んで検証する。
- 会社名
- アルパイン(株)
- 所在地
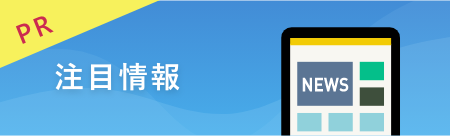
-
真空リフロー、N2リフロー、エアリフローのことなら、エイテックテクトロン(株)にお任せください。フラックスレス真空リフロー装置販売開始!エイテックテクトロン株式会社
-
独自の加工技術とノウハウで様々な材料にチャレンジ 〜色々なアイデアを生み出して研究者をサポート〜 ムソー工業株式会社 代表取締役 尾針 徹治 氏Gichoビジネスコミュニケーションズ株式会社
-
話題のGlass PKG実装技術の動向 〜先端電子部品への応用と 最新のCuダイレクトめっきGWCについて〜 Grand Joint Technology Ltd 大西 哲也(T. Onishi)Gichoビジネスコミュニケーションズ株式会社