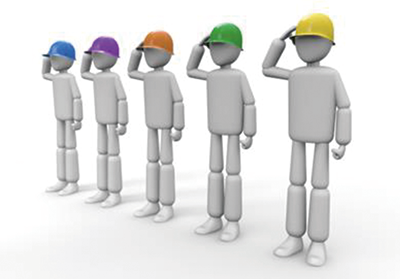
3.省人化
省人化とは、単位経済活動あたりの労働時間を減少させることであり、単位仕事あたりの人間の労力を減少させる省力化とは違った社会的影響がある。
作業改善や設備改善により、人を1人単位で省くことを省人化という。
一般の「省力化」では駄目だという意味をこめたトヨタ用語である。
先の例で言うと、「省力化」で 0.9 人分の仕事を減らしても 0.1 の仕事が残れば、その人は減らすことができない。確実に人が減ることを考えろ!という意味になる。つまり、確実に1人分の仕事を減らすまで改善しなければいけない。
これが省人化である。
省人化を行なうことができれば、この場合、1人をラインから抜き、他の仕事を担当してもらうことができる。1人分の固定費の削減だけでなく、他の業務を担当してもらえるわけであるから、効果としては2倍になる。
実際の改善活動では、省力化を行なったものの、省人化にはなっておらず、実際の成果(つまり利益)に結びついていないケースが多々存在している。改善活動においては、成果が 出なければ、自己満足と同じことになってしまう。成果が出ない自己満足を繰り返していると、収益は上がらない。そのため、頑張りが社員へ還元されることもなく、さらに社員のモチ ベーションは低下していく。
こうした事態に陥らないように省力化で満足せず、省人化まで行なうことを意識して、改善を進めていくことが大切なので ある。
ここで注意点!
「省人化に結びつかないから...、省力化にしかならないから ...、やっぱ、この改善はやらない」
こんな考えになっては駄目である(←でも意外と多いのが現状)。 最後は省人化へ繋げることを前提に、今できる省力化の改善を積み上げていくことが非常に重要なことなのである。
図2 省人化
4.少人化
最後に少人化である。これは、目のない省人化とも呼ばれている。 必要生産数に応じて生産性を落とすことなく、何人ででも生産できるラインを作りあげること。
生産ラインに配置される人を固定的に考えず、徹底的な合理化を行なって、生産量が少ないときは X人でできる仕組みを考える。多いときは Y人でできる仕組みを考えるなどのことになる。
まず大前提として、あたりまえのことであるがお客様の受注量は、毎月、毎週、毎日変動している。
であるので、必要な生産量は1週目は10人分の仕事、2週目は7人分の仕事、3 週目は9人分の仕事、というように、生産量も変動するのが普通である。
このような状況で、たとえば最大10人のラインにおいて、いつでも10人で造っていてはものが余ってしまい、造りすぎの無駄が発生したり、手待ちの無駄が発生してしまう(この7 つの無駄などについては別の回で説明する)。
そこで必要になってくる考え方が、少人化である。
少人化とは生産量の増減に応じて、最も少ない人数で対応することを言う。
大事なことは、7割の仕事しかない時は、7割の人員で作業できるようなラインを構築しなければならない、ということである。
先ほどのイメージ(10、7、9 人体制)を例にすると、
・10 人分の生産量の時は、10 人体制のライン
・ 7 人分の生産量の時は、7 人体制のライン
・ 9 人分の生産量の時は、9 人体制のライン
このように、自在に人員数を変動できることを目標とする。つまり、定員制からの脱却を行なうことが少人化である。 少人化体制が構築できれば、無駄が削減されて収益向上に直結する。 定員制ではなく、生産増減に応じて人員数を自在に変 更可能な少人化ラインをつくる!
これを達成するために、次のことを行なうことを参考にしていただきたい。
・標準作業を確実に構築すること(ルール作り)
・異なる複数の機械を扱えるようにすること(マルチ化)
・職場内、職場間の多能工を育てること(マルチ化教育)
まずは、標準作業をしっかりと構築しよう。その上で、どのライン配置でも作業ができる人材を育てていかなければならない。
そして、いつでも機械を移動できるような柔軟なレイアウトにすること、自在な生産ラインを構築するために工夫し続けることが大事である。
図3 少人化
- 会社名
- (一社)実装技術信頼性審査協会、STCソルダリングテクノロジセンター
- 所在地
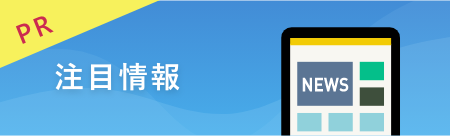
-
真空リフロー、N2リフロー、エアリフローのことなら、エイテックテクトロン(株)にお任せください。フラックスレス真空リフロー装置販売開始!エイテックテクトロン株式会社
-
独自の加工技術とノウハウで様々な材料にチャレンジ 〜色々なアイデアを生み出して研究者をサポート〜 ムソー工業株式会社 代表取締役 尾針 徹治 氏Gichoビジネスコミュニケーションズ株式会社
-
話題のGlass PKG実装技術の動向 〜先端電子部品への応用と 最新のCuダイレクトめっきGWCについて〜 Grand Joint Technology Ltd 大西 哲也(T. Onishi)Gichoビジネスコミュニケーションズ株式会社