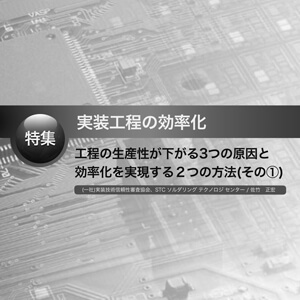
1. はじめに
・ 製造工程の効率化を行いたい
・ 工程を自動化して人手不足を解消したい
・ 効率化や自動化の注意点は?
今回は、このような製造業に関わる技術者や管理者として考えておきたいテーマについて説明する。
このテーマにおける2つのキーワードがある。
それは、「効率化」と「自動化」である。
労働人口が減少している現在、どの産業においても工程の機械化やロボットやAIを活用した、ファクトリーオートメーションの取り組みが急がれている。
しかし、やみくもに自動化を行っても、生産性を悪化させている課題箇所であるボトルネックが残っていてしまったり、工程自体の柔軟性が失われたりして生産上の都合が逆に悪くなったりする。
製造業で利益を上げていくためには、生産性を向上させることは必須になるが、自動化のために投資を行う以上、製造原価は上がっているので、それ以上のメリットの確保と自動化導入の弊害をなくすようにしなければ、取り組み自体が失敗してしまう。
今回は、工程の効率化が上手くいかない原因と効率化の方法を考えていく。
次回に、工程の自動化についての注意点を解説する。
2. 工程の生産性が下がる3つの原因
現在、製造業に求められていることを挙げると以下のようなものがある。
① 製品開発サイクルの短縮や短期化
② コスト低減
③ 製造納期の短縮
④ 品質向上
このように、いろいろな矛盾や無茶を求められているのが現状である。
「より良いものを、速く、安く、高品質な状態で作れ。」という理想に満ちた内容だからである。
しかし、現在の私たちの生活では特に不足しているものがないわけであるので、こういう要求が挙がってくるのも理解はできる。
ひと昔前のようにものがない時代ではなく、逆にものが余っている時代なのである。
顧客ニーズとしては、必要だから買うのではなく生活水準を上げるために買うという購買意欲に変化している時代なのである。
そこで、先ほどのように「より良いものを、速く、安く、高品質な状態で作れ」ような要求になるのである。 これが市場のニーズなのであるから、実現するために努力しておかないと将来的な経営にダメージが生じてくる。
そのためにも、効率化や自動化が必要なのである。
しかし、生産性を上げることが目的なのに、逆に下がってしまうケースとその原因がある。
代表的な原因を以下に3つ、紹介する。
3. 「人手不足」
団塊の世代の大量退職や、技術の伝承に時間がかかることから、技術職や技能職は圧倒的な人手不足である。 特に製造業では、深刻な人手不足に直面している。
経済産業省が日本の製造業の調査を行った「ものづくり白書2019」では、製造業における新卒者の就業人数は、ここ数年増加傾向にあるものの、10年以上の期間で見てみると10万人以上も減少しているようである。
特に従業員数300人以下の中小企業では、新卒者の就業者数が全国で30万人も減少しているなど、人材の確保が難しいのが現状である(図1)。
図1 製造業における企業規模別の新規学卒入職者数の推移(2019年版『ものづくり白書』「第3章 ものづくり人材の確保と育成」より引用)
これを受けて、一部の生産を海外工場に移管したり、国内工場に外国人労働者を活用するなどして、労働力不足に対応してきた。
しかし、海外においても少子高齢化や労働力の需要増加を受け、人材の確保が難しくなっているようである。 海外の調査でも、約半数以上の企業が人員確保に苦労していると回答している。
工場内の各工程を見てみても、必要な人員が確保できていないことがほとんどで、常にギリギリの人員で工程をまわしているのである。
有給などで欠員が出た日は、その工程に大きな負荷がかかり生産性を確保できていない。
現場は常に、人員補充を上長に訴えていることであろう。
しかし新しい人員を募集しても、そもそも労働人口が減少しているので、なかなか集まらない。
また、新しい人員が確保できたとしても、このような過酷な環境での作業が多いため、離職率が高いのが現状である。
人員も従業員の満足度も、どちらも確保できていないのである。
この課題が、他の原因にもかかわってくる大きな問題になる。
4. 「不良が多く、対策もできていない」
作業者によって技術レベルが異なるので、誰もが同じパフォーマンスを発揮できるわけではない。
技術レベルの格差から、作業ミスが生じやすいことも工程の効率化が進まない原因のひとつである。
とは言っても、先ほど説明したようにギリギリの人員で日々の生産をまわしているので、熟練の技術者から若手への技術伝承を行うだけの余裕がない。
何かしらの不良が発生した場合、熟練の技術者は不良の対策にコミットする時間が増え、そうしている間にも新たな不良の種が生まれたりしている。
いわゆる、「ハインリッヒの法則」である。
ちなみに「ハインリッヒの法則」とは、労働災害における経験則で「1つの重大事故の背後には29の軽微な事故があり、その背後には300のヒヤリハットが存在する」というものである。
熟練者と若手との技術格差を埋めるための、ノウハウの蓄積ができていないため、不良は多く、根本的な対策もできていないことが多いのが現状である。
作業を標準化していても、標準通りに作業を行う余裕がないことも原因と言えるであろう。
せっかく標準化した内容が、まさに絵に描いた餅になってしまっているのである。
5. 「セクショナリズムが強い」
製品の製造には、多くの部署が関わっている。
これら複数部署が連携して製品をより良いものにしていくのであるが、同じ会社のメンバーであるにもかかわらず、対立していまっていることが多々ある。
スムーズなコミュニケーションができていないのである。
コミュニケーションの場が、そもそもない、という場合もある。
こうした場合の生産現場は、対立している上流と下流の板挟みにあっている。
データの受け渡しミスや連絡ミスによって、生産のロスや不良が発生したりする。
しかし、製造したのは生産部門であるので、製造責任を問われる。
聞いてもいないことで怒られたり、謝罪する必要が出てきてしまうのである。
生産部門としては、やってられないだろう。
ますます対立は深くなっていくことになる。
このように部署間のセクショナリズムが強く、コミュニケーションが円滑でないことは、工程の効率化を阻害する原因といえる。
6. 効率化を実現する2つの方法
効率化を進めるための劇的な方法、というものはない。
むしろ誰もが知っていることを、愚直に行うだけである。
であるが、知っていることとできることは違うのである。
7. 「5S」
製造業に関わる人なら、誰もが知っている、社内ポスターの貼ってある「5S」である(図2)。
図2 5S
「整理」「整頓」「清掃」「清潔」「躾」の5つになるが、私個人としては「躾」という言葉が嫌いであるので、最後のSは「習慣化」や「スタンダード」のS、ということにしている。
「5S」は、そもそもはムダや無理、ムラをなくすための活動である。
しかし多くの企業では、あたりまえに整理整頓や掃除をするという理解で導入している。
しかし「5S」を行う理由を教えていないのである。
工程を本当の意味で効率化したいのであれば、「なぜ『5S』を行うのか」といった理由を理解したうえで取り組みを行う必要がある。
私も「5S」の外部講師として講演を行いるが、実に多くの企業が「5S」を本当の意味で活用できていないのが現状である。
「5S」と共に「ムダ取り」も重要になってくるが、過去の記事でムダ取りについては紹介しているので、今回は割愛する。
簡単にいうと、「5S」活動をさらに深掘りして動作分析を行う、という内容である。
8. 工程分析
工程を効率化したいのであれば、工程分析を行う必要がある。
工程内のどこかの作業に遅れが生じると、全体的な生産にも遅れが生じる。
そこがいわゆる、ボトルネックということである。
どこがボトルネックなのか、なぜ遅れるのか、遅れの原因は何か、といった内容を徹底的に分析することが必要である。
ボトルネックを改善することで効率化を図ることができるが、ここで止めてはいけない。
原因の改善と共に、工程内のレイアウトを検討することをおすすめする。
作業者や製品の導線を考えて、無理やムダのないように改善していくことが重要である。
ここまで改善が進むと見えてくるものがある。
それは、段取りのムダやムラである。
段取りにムダが生じていると、生産以外の時間が増えることになる。
それに、先ほど紹介した原因である他部署とのコミュニケーションの重要性や悪さが見えてくる。
これらを改善して生産性を向上し、工程の効率化を図っていくのである。
9. まとめ
今回は工程の効率化を進めるために、まずは生産性を下げる3つの原因として、
① 人手不足
② 不良が多く対策できていない
③ セクショナリズムが強い
の内容を解説した。
さらに工程の効率化を図る方法として、
① 5S活動の本当の意味
② 工程分析
について簡単に紹介した。
これらの内容が理解できて初めて、工場の自動化に繋がることになる。
逆にいうと、今回説明した工程の効率化を理解していないまま工場の自動化を進めると、ただ単にロボットやコンベアを導入するだけに終わってしまい(図3)、効率化できていないまま投資分だけコストアップしていることになってしまう。
図3 工程で稼働するロボット
次回紹介する予定の自動化とは、結局のところ今回の内容をロボット化したりAIを導入するだけなのである。
つまり自動化とは、「省人化や省力化を進め、人的ミスを減らし、生産性を向上すると共に効率化する」という内容なのである。
工場自動化における注意点や、自動化によって解消される従来の課題については、次回に詳しく掘り下げていきたいと思う。
- 会社名
- (一社)実装技術信頼性審査協会、STC ソルダリング テクノロジ センター
- 所在地
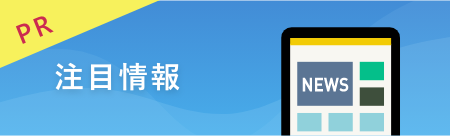
-
真空リフロー、N2リフロー、エアリフローのことなら、エイテックテクトロン(株)にお任せください。フラックスレス真空リフロー装置販売開始!エイテックテクトロン株式会社
-
独自の加工技術とノウハウで様々な材料にチャレンジ 〜色々なアイデアを生み出して研究者をサポート〜 ムソー工業株式会社 代表取締役 尾針 徹治 氏Gichoビジネスコミュニケーションズ株式会社
-
話題のGlass PKG実装技術の動向 〜先端電子部品への応用と 最新のCuダイレクトめっきGWCについて〜 Grand Joint Technology Ltd 大西 哲也(T. Onishi)Gichoビジネスコミュニケーションズ株式会社