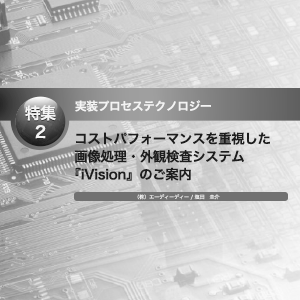
1. はじめに
2020年のUL796/796F STPは、昨年同様アメリカ カリフォルニア州サンディエゴのサンディエゴ コンベンションセンターで1月30日10:30から開催された(写真1)。
写真1
その頃はアメリカではインフルエンザの死者数が10,000人を超え、新型コロナウイルスよりインフルエンザのほうが懸念されていた時期であった。
日本では新型コロナウイルスの患者がまだ二桁になり始めた頃で、アメリカでも情報としては報道されてはいてもまだまだ深く認識されておらず、展示会でもマスクをしている人はアジア系の人くらいであった。
今回は、議題内容もあるが、日本からの参加者はごく僅かであった。
今回のミーティングでは、WEBを通して参加しているメンバーもいた。
今年のメンバー構成は表1のとおりである。
表1
今年のSTPは、UL796/746E関係が35件、UL 746F/796F関係が20件と、議題こそ多数あったが、その多くが用語の定義や規格の編集上の整備に関する内容であった。
ここでは、ここ数年懸念事項とされていた「積層板およびプリント配線板タスクグループのソルダリミット評価に関する要求の明確化」に関する議題の進捗を中心に述べたい。
昨年までと異なり、このソルダリミットに関するタスクグループのミーティングは欧米諸国の時間に合わせ、日本時間の22:00から開催されることが多かったため、日本からのタスクグループ参加者は毎回ごく限られていた。
STP開催前2~3ヶ月に行われたタスクグループのミーティングでは、主にFED(Association For Design, Circuit board and Electronics Manufacturing)とZVEI(ドイツ電気電子工業連盟)が作成した資料を元に議論が行われてきた。
FEDは、1992年にできた、ドイツ、オーストリア、スイスのメンバーからなる協会で、そのメンバーは、プリント配線板のデザイナーや製造メーカーから構成されている。
今回のミーティングでは、このタスクグループの議長であるCrystal VanderpanとJurgen Deutschmann (AT&S AG)が今までの調査結果について述べた。
2. ミーティングの概要
ミーティング中提示された「FEDとZVEIのマルチプルソルダリミットに関する提案」と題した資料から概要を示す。
1.背景
ZVEI、FEDとも、標準化作業に携わり、製品の安全性や信頼性に関わる業務を行っているが、ULのマルチプルソルダリミットの必要性に関しベース材料、レジストメーカー、配線板メーカー、アッセンブリーメーカーの代表者と話し合いを行った結果、次のような提案を行う。
2.アプローチ
現在多くの製品でマルチプルソルダが使用されている。
アッセンブリーの多様化や熱に関する個々のニーズの多様化から、ソルダプロファイルも個々に必要になってきている。
これはフロープロセスとリフロープロセスの両方にいえることである。
フロープロセスでは、熱負荷は配線板メーカーのテクノロジーと部品のスペック(260℃10秒のように)に制限され、TM650の2.6.8項に述べる方法で長年十分カバーしてきた。
リフローはこれより複雑化している。
ソルダペーストメーカーのスペックや、部品の温度の限度(最大245℃)、それと配線板の熱容量を考慮して個々のソルダプロファイルを作る必要がある。
このそれぞれのプロファイルの主な違いというのはピーク温度とはんだプロセスの時間である。
このため、リフロープロセスに統一した最大プロファイルを決めることはできない。
実際には、時間が長いものは、ピーク温度が低いプロファイルになるが、時間が短いプロファイルはピーク温度が相対的に高くなる。
従って、重要な要因になるのが、プリント配線板から発生する熱量である。
これはKs(Kelvin seconds)で規定するが、これは簡単に言うとプロファイルのカーブの面積になる。
3.結果
リジッドの場合には下記が当てはまる。
特別な形状(フレキ、リジッドフレキ、IMS)や特殊な材料(つまりポリイミド)の場合には、ソルダリングパラメーターはPCBメーカーと部品の製造業者とで同意したものでなくてはならない。
この同意したプロファイルと温度サイクルの回数をULに連絡し、試験をしてもらう。
アッセンブリーメーカーのデータ要求では、プリント配線板の温度負荷を代表する3つの重要なプロファイルがあることがわかった。
a. IPC-TM-650の6.2.27Aに基づくプロファイル
b. パワーエレクトロニクスのモジュールではJ-STD-020と同じプロファイル
c. 30℃以上になる最初と終わりの温度で105,000Ksを超えない熱量
これらのプロファイル、および、発生する熱容量の計算方法の例を図1、図2に示す。
図1
図2
図3、図4の3つのプロファイルに、アッセンブリーメーカーで使用するプロファイルを包含することができる。
また、プリント配線板を2つのカテゴリーに分けることも理にかなっている。
個々のベース材料の選択を行う際には、はんだプロセスの回数とその後のアッセンブリーに依存している。
■カテゴリー1
はんだプロセスがほとんどないプリント配線板。
アッセンブリーでの負荷が低いことにより、判定基準は低くしなくてはならない(たとえば3回だけのリフローシミュレーション)。
■カテゴリー2
たとえばリフロー2回、フロー2回というようないくつかのはんだプロセスを行うプリント配線板。
この場合には、TM-650 20.6.27A(図3)に述べるようなシミュレーションを行う。
図3
ミーティング中、特に反対を示す意見はなく、4月10日付けで事前レビューのための提案が出され、5月1日にコメントが締め切られたが、特に反対意見はなかった。
表2が現状ULで提案しているサーマルストレスの方法である。
表2
基本は260℃で6回となっているが、245℃・230℃を選択することもできる。
会議参加者からは、260℃で6回実施すれば、プリント配線板の99%はカバーすることができるというコメントもあった。
果たしてアッセンブリーメーカーでどのようなはんだプロセスを実施するのかは実情を把握できない現状では、オプションの方法であるとはいえこの方法を取り入れざるを得なくなるであろう。
最後に今回の追加議題として、Ventec Intrnational GroupのAlun Morgan氏からた、プリント配線板を化学組成からではなく性能ごとに分類して、代表となるものを一つ試験すれば、同等の性能を保つ他の基板は試験無しで使用できるようにしようという提案があった(図4)。
図4
基板メーカーの見地からのユニークな提案である。
当提案を含め、今回、表3に示す3つのタスクグループが設けられた。
表3
- 会社名
- (株)ケミトックス
- 所在地
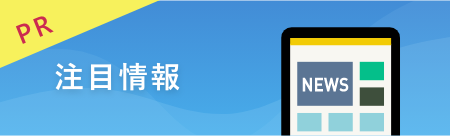
-
真空リフロー、N2リフロー、エアリフローのことなら、エイテックテクトロン(株)にお任せください。フラックスレス真空リフロー装置販売開始!エイテックテクトロン株式会社
-
独自の加工技術とノウハウで様々な材料にチャレンジ 〜色々なアイデアを生み出して研究者をサポート〜 ムソー工業株式会社 代表取締役 尾針 徹治 氏Gichoビジネスコミュニケーションズ株式会社
-
話題のGlass PKG実装技術の動向 〜先端電子部品への応用と 最新のCuダイレクトめっきGWCについて〜 Grand Joint Technology Ltd 大西 哲也(T. Onishi)Gichoビジネスコミュニケーションズ株式会社