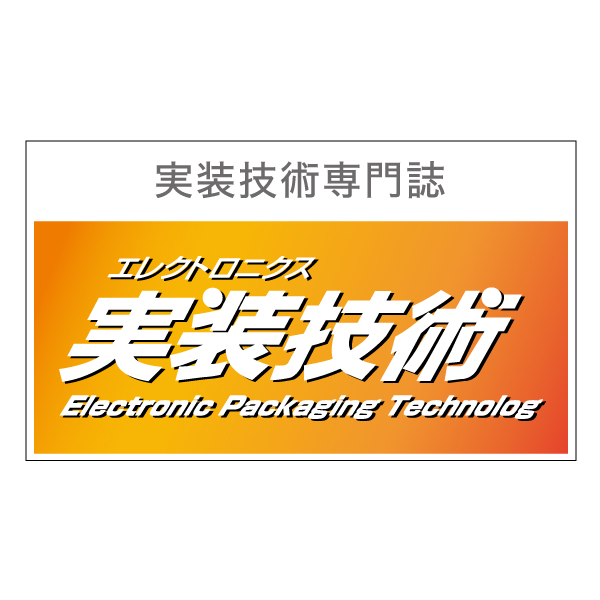
①はじめに
約160年前の1864年にイギリスの科学者であるマクスウェルが電磁波の存在を予言し、わずか40年後には無線機が実用化された。その後の100年間でラジオやテレビなど電磁波を利用した電子機器が広く普及し、ほぼ時を同じくして急速に進歩したコンピュータ技術と相まって、2020年では国内のモバイル端末全体の世帯保有率は95%を超えるまでになった(図1)。
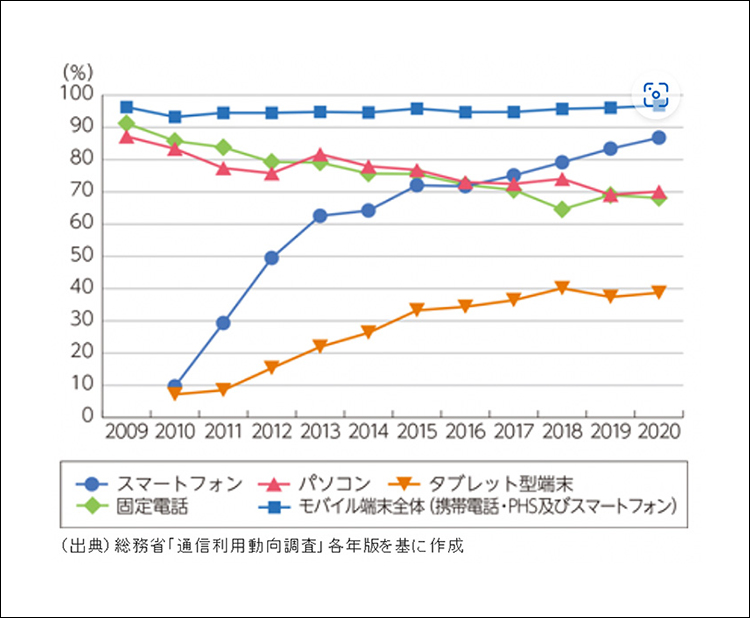
図1 情報通信機器の世帯保有率
ここまで急速に発展した背景には、一つには1960年代に表面実装可能な電子部品(SMT部品)やクリームはんだ(ペーストはんだとも言われる)などが出現し、チップマウンタ(表面実装機)と呼ばれる実装機械が出現し実装技術が完成したことで、電子機器の大量生産が可能になったことがある。さらにはエレクトロニクスの大きな飛躍、すなわちプリント配線板はもとより半導体や電子部品、電池などの小型化・低背化・高性能化がある。換言すると、エレクトロニクスが社会の文化的および経済的な発展に大きく寄与してきたということになる。人間に例えると、頭脳を司るのがCPUで、心臓など各内臓がICとすると、それらを支える背骨および信号やエネルギーを伝える神経および血管がプリント配線板となるであろう。さらにはプリント配線板なしには、エレクトロニクスの発展は成し得なかったであろうともいえる。以下プリント配線板の進化に注目する。
②プリント配線板の誕生と成長
資料によると、プリント配線板の原型は1936年に銅箔を薄い紙やキャンバスに貼り、そこに回路を構成する方法がオーストリア人の発明家Paul Eislerにより考案された、とある。一方、日本でも同年、宮田喜之助氏がプリント配線板の特許を出願したと書かれている。いずれもこの時には実用化はされなかったが、太平洋戦争後になり米国にてめっきスルーホール技術が発明され、トランジスタラジオに採用されて実用化に至った。その後は多層化やビルドアップなどプリント配線板の進化が進み、小型通信機器やスーパーコンピュータなど最先端電子機器には欠かせない部品となった。 このようにプリント配線板の技術は我が国のエレクトロニクスがここまで進化させてきたといってもいいだろう。またプリント配線板は時代が進むに従い種類も機能も増えてきた(図2)。

図2 プリント配線板の種類
以下、プリント配線板の種類と構造を簡単に紹介する。
プリント配線板にはリジッド基板とフレキシブル基板がある。この二つは用途、性質、構造、材料、製造方法など全く異なるため、違う部品とみなすことができる。
今回はリジッド基板に関して解説する。
1. 片面基板(図3)
基板の片側の面にのみ回路を形成する配線板。電気回路は二次元であり、立体交差になるような回路はできない簡単な配線板。
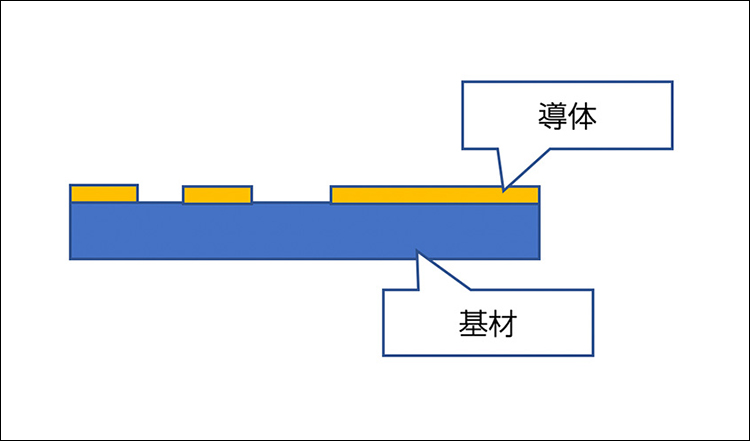
図3 片面基板
2. 両面基板(図4)
基板の両側の面に回路を形成する配線板。立体交差の回路を形成でき、片面基板より複雑で高密度の回路が可能になる。両方の面を電気的に結合するためには、貫通穴をあけ内部の側壁をめっきあるいは金属で両側を導通させる手段がある。

図4 両面基板
3. 多層基板
配線層が複数ある配線板である。多層基板は基板サイズを小型化するときに用いられる。高周波用として多層基板を用いる場合は一般的にいずれかの配線層には回路を作らず、そのままでグランド層(ベタアース)とするケースが多い。
多層基板は、構造と製造方法の違いにより、①貫通多層基板、②IVH(interstitial via hole)多層基板、③ビルドアップ基板の3種類がある。
(1) 貫通多層基板(図5)
図に示すように導体と絶縁体を複数重ねて多層基板とし、貫通穴(スルーホール)をあけて、各導体間に導通を持たせる構造である。層数は何十層にもなっているものもある。電子機器の小型化に寄与している。
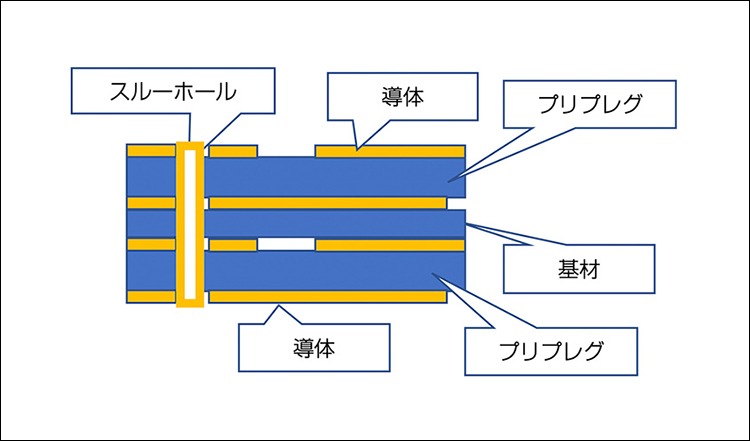
図5 貫通多層基板
(2) IVH多層基板(図6)
穴を貫通させずに必要な層間のみを図のように接続した構造の配線板がIVH多層基板である。これにより複雑な回路構成も可能となった。表面層からの非貫通穴をブラインド・ビア・ホールと呼び、内部だけの非貫通穴をベリード・ビア・ホールという。
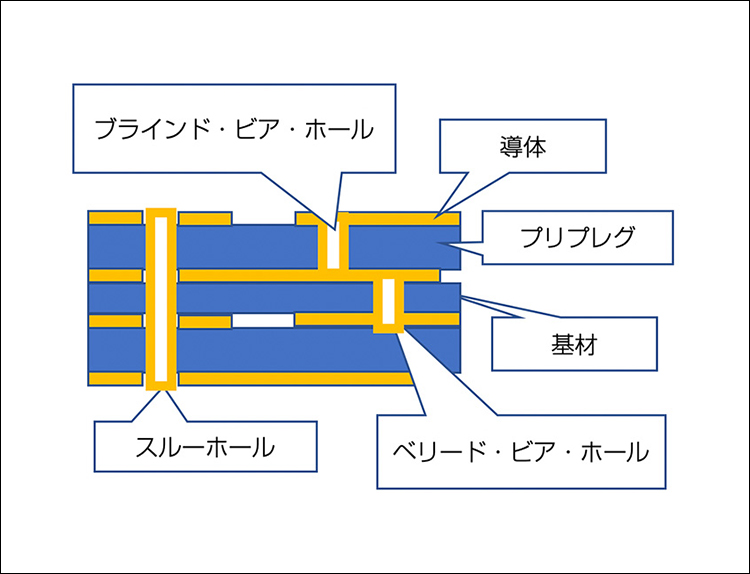
図6 IVH多層基板
(3) ビルドアップ基板(図7)
ビルドアップ基板とは積み重ねにより、製造された多層基板のことである。基本になるIVH基板(コア層)にプリプレグと導体を重ね、必要な場所へレーザで穴あけを行い、各層を導通させて層を重ねていく配線板である。レーザで開けた穴をLVH(Laser Via Hole)という。
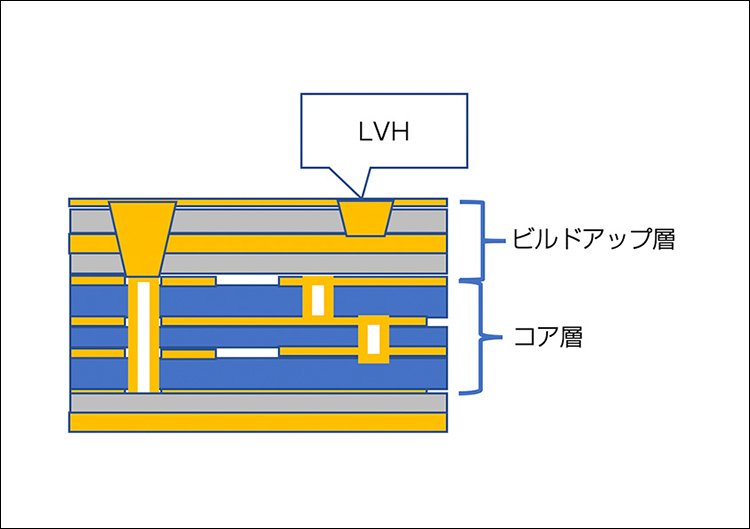
図7 ビルドアップ基板
③プリント配線板の主な基本技術
代表的なプリント配線板の構造は上記図3〜図7に示す通りである。銅箔を基材に貼り付け、回路をエッチング等で構成する構造で、一見単純なように見えるが、プリント配線板が発明された当時とは異なり、多層構造や部品内蔵、あるいはテラヘルツ帯などの超高周波対応など、現在の最先端技術はプリント配線板に難易度の高い仕様要求を出している。
これら要求仕様に対応させる最先端技術の開発は容易ではないことがわかる。一般的に単純なものを高性能化することほど難しいということが多々あるが、プリント配線板も高品質を維持して、高性能の製品を作るのは高い製造技術力と蓄積されたノウハウが必要である。特に高周波領域を扱う製品ではプリント配線板の完成度次第で高周波機器の性能および品質が大きく影響してくる。
以下プリント配線板にとって主要と思われる技術を紹介する。
1. 絶縁材料技術
プリント配線場の主材料としては基材となる絶縁材料、導体となる銅箔の技術、はんだレジスト材料などがある。基材には各種材料が用いられており、絶縁体の材料別種類を以下に解説する。
(1) 紙フェノール基板(FR-1、FR-2)
紙にフェノール樹脂を含浸させた材料で製造したプリント配線板であり、主に片面基板に使用されている。
加工性が高く低コストであり、リモコンなど民生用機器に多く使われている。反面熱や湿気に弱く、反りやすく機械的強度が低い点が短所である。スルーホールには不向きである。紙ベースの配線板は市場では縮小傾向にある。品名のFR(Flame Retardant)は銅張積層板の難燃性を表しており、その後に続く数字が大きいほど難燃性に優れることを意味している。
(2) 紙エポキシ基板(FR-3)
紙フェノール基板と同様に片面基板に使用されている。
上記の紙フェノール基板に比較して耐熱性や吸湿性、絶縁抵抗、高周波特性などの点で優れており、高電圧回路や耐湿性が求められる回路に使われることが多い。スルーホール形成が可能である。
(3) ガラス布/ガラス不繊布エポキシ樹脂
(CEM-3 : Composite epoxy material-3)
ガラス布とガラス不織布を混ぜ合わせた基材にエポキシ樹脂を滲みこませたもの。
片面基板では対応できないような家電品から産業機器まで両面基板の広い範囲で使用されている。一般的にエポキシ樹脂には吸水性があるため、プリント配線板の保管方法に注意が必要である。水分を含んだ材料は、はんだリフロー炉で加熱された際に、水蒸気爆発を起こす可能性があるためである。
(4) ガラス布基材エポキシ樹脂(FR-4、FR-5)
ガラス繊維を布状に編んだガラス織布にエポキシ樹脂を滲みこませたもの。
銅箔厚も各種材料があり、汎用性も高く両面基板のほかに多層基板にも使用されている。携帯電話をはじめコンピュータ関係など、現在もっとも一般的であり、広い市場で用いられている。
(5) ガラス布基材ポリフェニレン・エーテル樹脂
(PPE:Polyphenylene Ether)
PPEは引張強さ、降伏強さ、弾性率などの機械的性質に優れ、温度や湿度の変化に影響されにくい。かつ広い周波数域に対し比誘電率や誘電正接が小さい、など工業製品用樹脂として適している材料である。樹脂をガラスクロスに含侵させて使用される。ミリ波よりも少し低い周波数帯で利用されることが多い。
(6) テフロン樹脂(PTFE : Polytetrafluoroethylene)
テフロン(フッ素基板)は不燃性で非常に高い絶縁性と低い比誘電率を示すため、5G用など高周波特性が求められる回路で主に使用されている。
(7) LTCC(Low Temperature Co-fired Ceramics :
低温同時焼成セラミックス)
比誘電率は有機材料に比して大きいが、誘電正接が十分小さいのが特徴である。比誘電率が比較的大きいため小型化に適している。そのためAiP(Antenna in package)など小型モジュールに採用されている。
2. 導体材料技術
導体材料は銅箔を用いるのが一般的である。回路形成には銅箔をエッチング加工して行う。銅箔は基材に貼られるのであるが、はがれては困るため、銅箔の張り合わせ面を粗化し、接着強度を増している。後述するが近年通信機器は高周波化が著しく、高周波信号の表皮効果により信号電流が銅箔の表面しか流れないため、粗化加工が伝送損失に悪影響を与えるようになってきた。そのため、銅箔の表面をできるだけ平らにし、鏡面状にする必要がある。このことは接着強度に反するため、鏡面状の銅箔で接着強度を保つことができるような技術開発が進んでいる。
3. 穴あけ技術
プリント配線板には搭載する電子部品のリード線などを通すための貫通穴や、両面基板や多層基板へスルーホールを作るため穴をあけなくてはならない。ドリルを用いて機械的にあける方法と、ビルドアップ基板などの電気的導通のための小さな穴(viaと呼ぶ)はレーザであける。最小のドリルは径0.1mmのものもある。精密微細加工と言える。穴あけ後はバリ等を除去するデスミアという加工を行う。
4. エッチング技術
銅箔に回路を形成するために、エッチングを用いている。フォトリソグラフィと呼ばれる写真現像技術が用いられる。近年回路形成に細線が要求されてきており、微細化エッチング技術が開発されてきている。
5. めっき技術
上記「4.エッチング技術」の対極にある技術である。エッチングは金属部分を化学的に削り取る技術であるが、めっきは金属を対象物の表面に形成する技術である。めっきは大別して電解めっきと無電解めっきがある。めっきに用いる金属は回路形成用の銅(Cu)をはじめ金(Au)、ニッケル(Ni)、すず(Sn)、銀(Ag)など多々ある。スルーホールの導通化やブラインドビアもめっきで作られる。
以上、簡単に主なものを紹介したが、実際にプリント配線板を作るためには、膨大なノウハウと技術が必要である。
- 会社名
- 特定非営利活動法人 サーキットネットワーク
- 所在地
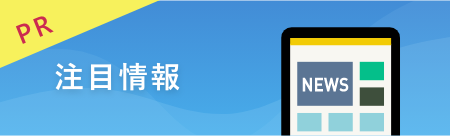
-
真空リフロー、N2リフロー、エアリフローのことなら、エイテックテクトロン(株)にお任せください。フラックスレス真空リフロー装置販売開始!エイテックテクトロン株式会社
-
アレムコの導電性/熱伝導性接着剤,コーティング材,グリースのことなら(株)エス・エス・アイ株式会社エス・エスアイ
-
独自の加工技術とノウハウで様々な材料にチャレンジ 〜色々なアイデアを生み出して研究者をサポート〜 ムソー工業株式会社 代表取締役 尾針 徹治 氏Gichoビジネスコミュニケーションズ株式会社
-
SEMICON Japan 2023 2023年12月13日(水)〜15日(金)の3日間、東京ビッグサイトにおいて、半導体を中心としたマイクロエレクトロニクスの製造を支える装置/材料産業の総合イベントであるSEMICON Japan 2023が開催された。Gichoビジネスコミュニケーションズ株式会社