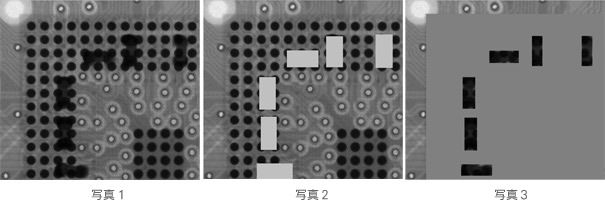
実装基板現場の要求
BGA(Ball Grid Array)が発表されたのは、1990年頃であった。当時はQFP(Quad Flat Package)の狭ピッチ化がさかんで、インチ規格の1.27mmピッチから日本規格の1.0mmピッチへと縮小されてからは、0.8mmピッチ、0.65mmピッチ、0.5mmピッチへと一気に狭ピッチ化へと進んだ。しかし、0.5mmピッチ以下は歩留まりなどの問題で普及せず、BGAへと徐々に移行していった。
BGAが出現してからすでに20年の年月が経過するが、製造工程中の自動検査はいまだに確立されていないのが現状である。
BGA実装が始まった当初から1995年頃までは、ピッチ間隔も1.27?1.0mmと大きかったこともあり、それまで0.5mmピッチQFPに対応していた実装現場にとって難しい実装ではなかった。またBGAのはんだボールが大きい(φ0.75mm)こともあり、セルフアライメントが効くことも大きな要因であったものの、1996?1997年以降には、BAGのボールピッチ間隔が0.8mm以下のファインピッチ化が進むようになり、BGAの自動検査のニーズも高まってきた。
しかし当時は実装基板用のX線検査装置は高価な海外製品が主流を占めていた。米国のNicolet社(現・テラダイン社)やHP社のインラインX線検査機であった。どちらの装置も購入価格は7千万円から1億円近くと大変高価なシステムであり、よほどの高付加価値の基板でなければ導入することはできなかった。
実装現場からはX線装置は高価すぎる、これでは導入できない。といった声が多く聞かれた。
筆者自身、そのNicolet社の日本代理店の営業としてお客様を廻る中で直接その現場の声を聞き、どうにかならないものかと考えた。そして、そういった現場のニーズに答えるべきだとして、2000年に、アイビットをX線検査装置メーカーとして設立したのである。
実装現場の要求としては、
①設備価格としてはAOI(Automated Optical Inspection=外観検査機)と同等レベル
②高速検査を可能としインラインを可能とするもの
③ランニングコストとしてはなるべく低く
④24時間×365日間、安定稼動できるもの
⑤設置面積はなるべく小さく
⑥データ作成が簡単なこと
などがあった。
表1 インラインX線検査機の性能/価格表
当社ではこれらの要求を満たすために設立時から実装基板用のX線装置の開発を行ってきた。そして今回、新方式『X線ステレオ差分方式』の開発に至った。
今回はその現場の要求に応えるべき製品として発表した『X線ステレオ差分方式』について紹介する。
表1は、現状のX線検査機の性能と価格である。
従来X線検査機の長所/短所
X線の利点でもある透過視ができることで、BGAのはんだボール部を透過検査することができた。しかし、両面実装の場合、両面が1画面に写ってしまうことが欠点であった(写真1)。
この状態では裏面と重なり合った部分がBGAのボール間を埋めてしまうため、まるでブリッジ不良であるかのような検査画像となってしまう。正しい検査を行うためには、両面実装部品をおのおの分ける必要があった。
図1 マスター画像引き算方式
従来方法の解決策としては、以下のような手法をとっている。
①この部分を画像処理し反対色で塗ってマスクする手法などがある(写真2)。
→しかし、マスクした部分は検査除外箇所となり、高密度実装になればなるほど検査除外箇所が増え検査が難しくなる。
②片面実装(チップのみ実装)した状態でX線検査機 に投入しマスターデータを作成し、その画像を両面実装した画像から引き算をする(写真3)。
→しかし、チップ部品を画像処理で引き算し、除外した場所は、検査に必要な輝度情報が得られず不検出エリアとなり結局はマスクする手法と変わらず、検査が難しかった(図1)
この場合、両面実装部分をおのおの分けるという よりは、見たくない部分(検査したくない部分)を 隠した。という状態であったが、これは実装現場 の要求を満たしたことにならず、X線検査が普及しない原因ともなっていた。
- 会社名
- (株)アイビット
- 所在地
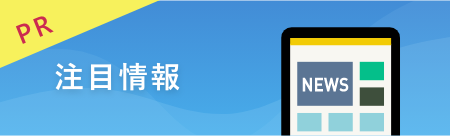
-
真空リフロー、N2リフロー、エアリフローのことなら、エイテックテクトロン(株)にお任せください。フラックスレス真空リフロー装置販売開始!エイテックテクトロン株式会社
-
独自の加工技術とノウハウで様々な材料にチャレンジ 〜色々なアイデアを生み出して研究者をサポート〜 ムソー工業株式会社 代表取締役 尾針 徹治 氏Gichoビジネスコミュニケーションズ株式会社
-
話題のGlass PKG実装技術の動向 〜先端電子部品への応用と 最新のCuダイレクトめっきGWCについて〜 Grand Joint Technology Ltd 大西 哲也(T. Onishi)Gichoビジネスコミュニケーションズ株式会社