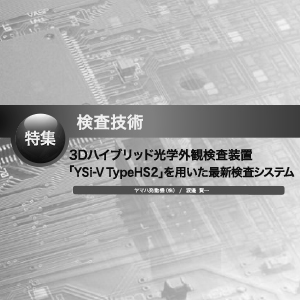
1. はじめに
昨年から続く、新型コロナウイルス感染症の世界的流行により、私たちの日常は一変した。
多くの企業ではテレワークを導入し、WEB会議やクラウドサービスを用いたデータの共有があたりまえとなった。
学校では、オンライン授業が行われ、プライベートでのコミュニケーションにおいては、SNSやテレビ電話がより一層浸透した。
これらの変化により、ネットワーク環境を構築するための通信インフラの重要性は増し、5G関連をはじめとする、様々な通信機器に対しての品質意識は高まりつつある。
上記を背景とし、自動車や医療機器といった従来から高い品質を要求される分野以外の製品に対しても、高品質化を求める声は高まり、電子基板生産において品質保証の役割をもつAOIに関しても、より高機能なものが必要とされている。
当社では、3Dハイブリッド光学外観検査装置『YSi-V 12M TypeHS2』を、2017年にリリースし、その後もバージョンアップを続けることで、2021年現在においても、最先端のSMT生産ラインの品質、及び生産性に追従できる3D AOIとして、多くのお客様のSMT生産工程にてご使用頂いている(写真1)。
写真1 3Dハイブリッド光学外観検査装置『YSi-V 12M TypeHS2』
2. 3Dハイブリッド光学外観検査装置『YSi-V 12M TypeHS2』の新機能
『YSi-V 12M TypeHS2』は、実際に使用されるお客様の声をもとに、進化を続けてきた。
今回は、下記の新たな3つのソリューションに関して、紹介する。
(1)AI 検査ライブラリ自動マッチング
(2)「DIP基板データ自動作成
(3)N点照合
1.AI検査ライブラリ自動マッチング
「生産現場で、AIを活用する」という言葉を良く耳にするが、本当にAIを活用できている例は非常に少ない。
今回、『YSi-V 12M TypeHS2』では、AIの Deep Learningを活用することで、もっとも手間のかかる検査機のデータ作成の多くの作業を自動化することに成功した。
AOIを使用して電子基板の検査を行うためには、何千点も搭載されている様々な形状の部品に合わせて、適切な検査データを1つ1つ作成する必要がある。
この部品ごとの検査データを作成する作業は、SMTラインを構築する装置の中でも、もっとも大変な作業の1つであるといえる。
『YSi-V 12M TypeHS2』では、「標準検査ライブラリ」という各部品形状に応じた検査データを予め用意しておき、検査対象の部品に合致するデータを選択することで、検査プログラムを簡単に作ることができる。
この検査プログラムの作成方法は、他の従来のAOIに比べると、非常に優位性のある手法であったが、この「各部品に対して正しい標準検査ライブラリを選ぶ」という行為に時間がかかってしまっていた。
当社では、この問題を解決するために、 AIのDeep Learningを活用した新機能を開発した。
大量の部品画像をDeep Learningを用いて、予めAOIのプログラミングソフトへ学習させておくことで、『YSi-V 12M TypeHS2』 で撮像した2Dと3Dの部品画像から自動的に部品タイプや形状を判別し、最適な検査データが自動的に選択され、検査プログラムを完成させることが可能となる。
この機能を開発したことで、検査すべき基板の画像を1度AOIのカメラで撮像するだけで、検査プログラムの大部分を完成させることが可能となり、検査プログラム作成の作業効率を大幅に向上させることができるようになった(図1)
図1 AI 検査ライブラリ自動マッチング
2.DIP基板データ自動作成
DIP工程による基板生産は、SMT工程が主流となった今でもなくなることはない。
また、これらの基板検査に関しても、AOIによる検査が必要とされており、最近では、3D AOIを導入することも非常に多くなってきている。
DIP基板の検査に関しても、やはり検査データの作成が大変な作業として挙げられる。
特にSMT工程の基板とは違い、電子部品を載せた裏側のリード部分のはんだ付け検査となるため、検査したい箇所の座標データが無いというようなことがある。
このケースに遭遇すると、検査データは実際の基板を見ながら、座標を打ち込むところから始めなければならないため、検査データの作成に非常に多くの時間を費やしてしまうことになる。
この課題を解決するため、『YSi-V 12M TypeHS2』では、撮像した基板画像から自動的にスルーホールの個所を特定し、座標データの作成から検査ライブラリの貼付けまでを行う機能を開発した(図2)。
図2 DIP基板 自動データ作成
この機能を活用することで、CADデータを満足に用意することができない基板に関しても、効率的に検査データを作成することができるようになるため、DIP基板に対しても高品質な生産が実現できる。
3.N点照合
SMT工程において、同一ラインを構成する異なる生産装置間での連携機能を導入することが増えてきている。
当社では、印刷機、マウンタ、検査装置とSMT工程を構成する主要設備を1ブランドで揃えることができる「1 Stop Smart Solution」を掲げており、高度なM2M連携の機能開発を積極的に推進し、より高効率で高品質な生産に貢献できるように努めている。
その機能群の中でももっとも幅広いユーザーから高評価を得ている機能が「N点照合」である。
この「N点照合」という機能は、不良が発生した際に、その不良に関する各工程の画像、及びエラーなどのイベント情報を自動的に検索し、同一画面上に表示することで、「どの工程で」不良が発生したのかを即時に判断することができるようにする機能である(図3)。
図3 N点照合
最終工程であるAOIが不良を検出した際、その不良となった部品のリフロー炉に入る前の状態や、マウンタ実装時の吸着状態、はんだ印刷後の状態などが分からないため、不良発生の原因となる工程が特定できず、根本原因の解決に至らないというケースが非常に多くある。
しかし、N点照合があることで、その不良基板を生産していた時の実際の各工程の画像を映し出すことができるため、リフロー前の基板の状態や部品の認識画像、作業イベント情報などから、どの工程の誰が作業しているときに、その不良が発生したのかを特定し、具体的な改善アクションへつなげることができるようになる。
この機能により、不良発生時の工程改善は大きく前進し、工程内不良率の向上に貢献できる。
3. リフロー前検査への3D AOIの活用事例とその効果
当社では、高品質なSMT生産ラインを実現するためには、リフロー前にAOIを設置し、リフロー前検査を行うことを推奨してきた。
近年の高品質化の要求に伴い、リフロー前検査を導入するお客様も、以前と比較して増加傾向にある。
今回は、リフロー前検査を行う装置を3D AOIにした場合、どのようなメリットや品質改善効果があるのかを、実際の生産の品質結果の比較を用いて紹介する。
1.AOIによるリフロー前検査のメリット
リフロー前検査は、最終品質保証の役割を担うリフロー後の検査に比べると、必要性が低いと判断されやすく、導入しづらい面があるが、実際には生産において多くのメリットをもたらす工程となる。
リフロー前検査の導入には、大きく3つのメリットが存在する。
まず1つ目は、単純に「リフロー後の不良発生数が減る」という点である。
完成基板の不良の修正は職人的なスキルを必要とする作業であり、対応できる作業者は限られる。
特に、ピン数の多いICやコネクタなどの不良においては、修正作業は非常に難しく、作業にかかる時間も大きなものとなる。
また、修正に失敗した場合には、完成基板自体を廃棄しなくてはならなくなり、ロスコストに繋がる。
リフロー前検査を導入することで、これらのリフロー後で発生する不良の数量は格段に少なくなり、作業工数や廃棄コストの面でのメリットが見込める。
2つ目は、「検査機の直行率の向上」である。SMT工程のAOIでは、必ず「過判定」が発生する。
「過判定」とは、実際には、正常品であるが、AOIが不良品と間違った判定をしてしまうことである。
従って、AOIが不良と判定した部品は、すべて人が再度判定を行い、本当の不良品と正常品を仕分ける作業が必要となる。
3D AOIになって、「過判定」はかなり少なくなってきているが、0にすることは非常に難しいため、いまだに人による再判定の作業が必要となっている。
特に、過判定しやすい検査の1つとして、極性検査や文字検査といった、ICなどのモールド部品の表面に印字されている文字やマークを読み取るという検査が挙げられる。
リフロー炉の中では、クリームはんだに含まれているフラックスなどが飛散するため、リフロー後のIC表面にはフラックスが付着し、文字やマークが消えかかってしまっていることがあり、それによってAOIで正常に読み取ることが困難となり、結果として「過判定」を発生させてしまう。
この問題は、リフロー前で極性検査や文字検査をしてしまうことで解決する。
リフロー前では印字は非常に綺麗な状態であり、過判定の発生は大幅に削減される(図4)。
図4 リフロー前後の検査画像-1
これにより、AOIをインラインして再判定をしている場合は、再判定待ちによりラインの稼働率を落とすリスクを低減できる。
また、オフラインで再判定する場合にも、再判定の作業自体を減らすことができ、SMT工程全体としてメリットを享受することができる。
3つ目は、「不良発生原因を特定しやすくなる」という点である。
N点照合の際にも触れたが、各工程の画像が残っているということは、発生した不良の原因を追及する際には、非常に役に立つ。
リフロー前検査を行っている場合、リフロー後で発生した不良が、リフロー前ではどのような状態だったのかが確認できるため、マウンタが不良を発生させたのか、それ以降の工程で不良を発生させたのかがすぐに判断できる(図5)。
図5 リフロー前後の検査画像-2
この画像がないと、マウンタが位置ズレを起こしたのではないかという推測のもと、まったく問題を起こしていないマウンタに対して無駄な確認や検証を行うという的外れな改善作業を行うことになる。
工程品質を効率的に引き上げるためには、リフロー前検査は非常に有効な良いツールとなる。
2.リフロー前検査用のAOIを選定するポイント
では、リフロー前検査を行うAOIは、どのような点に注意して選定したらよいだろうか。
性能、構造、作業効率の3つにおいて確認すべきポイントを説明する。
まず、性能においてであるが、やはりリフロー前検査として必要な機能が充実していることが重要である。
リフロー前検査では、はんだ付けの検査をしないため、欠品や位置ズレの検査が中心になるが、3D AOIになるとこれらの検査は比較的に簡単な検査となるため、各AOI間の差はほとんど感じられないと思われる。
従って、比較的難しい検査となる極性検査や文字検査の性能が優れているAOIを選ぶと良い。
また、リフロー前検査は、マウンタとの連携機能との相性が良いため、M2M連携機能が充実しているかどうかも重要な要素となる(図6)。
図6 マウンタ連携機能
次に、構造であるが、リフロー前検査では、部品が基板へはんだ付けされていない状態であるため、コンベア側が駆動して検査するAOIは望ましくない。
コンベア側が駆動すると、部品の位置ズレなどを引き起こす可能性があるためである。
現在、販売されているAOIは検査ヘッド側が駆動するタイプがほとんどであるが、旧装置などを流用する際には注意が必要である。
最後は作業効率に関して説明する。リフロー前後で活用するAOIは、検査データの互換性があることが望ましい。
もちろんリフロー前後では基板の状態も検査したい内容も異なるため、完全に検査データを流用することが困難ではあるが、ベースとなる検査データが流用できるだけでもデータ作成にかかる作業時間は大幅に短くなる。
従って、リフロー前検査を検討する場合には、リフロー後のAOIも併せてどのAOIが良いのかを検討するとより良い選択ができるようになる。
3.リフロー前検査の形態によるリフロー後の品質比較
最後に、実際にリフロー前検査を行うことで、リフロー後の品質がどの程度良くなるのかを実際の生産ラインの品質状況から比較してみる。
当社では、お客様の見学、及び開発装置の検証用の生産ラインを保有しており、リフロー前後に3D AOIを導入している(写真2)。
写真2 リフロー前 3D AOI
このラインの2019年11月から2020年10月までの品質結果より、リフロー前の検査を「なし」、「2D AOI」、「3D AOI」としたときに、リフロー後の部品搭載点数あたりの平均不良率がどの程度改善されるのかを紹介する。
まず、リフロー前にAOIを入れていない場合の不良率であるが、年間通しての平均不良率は4.16ppmとなった。
不良率の一番悪い月は6.02ppmで、一番良い月は、2.75ppmとなっており、毎月不良が発生しているという状況である。
次に、「2D AOI」をリフロー前に入れた場合は、平均不良率は、1.40ppmまで改善された。
リフロー後の不良発生数はおよそ、3分の1程度に抑制される。
不良率が0ppmの月が1回発生しており、大幅にリフロー後の不良率が改善されることが分かる(図7)。
図7 品質推移 (リフロー前検査なし / リフロー前 2D AOI)
最後に、「3D AOI」をリフロー前に入れた場合であるが、平均不良率は、0.73ppmまで改善された。
リフロー前に「2D AOI」を入れていたときに比べて、不良の発生数はおよそ半分になる。
このことから、導入する生産ラインの元々の品質状態にも依るが、リフロー前検査をすることで、大幅にリフロー後の品質状況を改善することができるということが分かる(図8)。
図8 品質推移 (リフロー前2 DAOI / リフロー前 3D AOI)
なお、リフロー前に3D AOIを導入したとしても、リフロー前では外観上問題がないが、リフロー後になると発現する不良も存在するため、リフロー後のAOIは、品質保証の観点から考えれば、引き続き必要である(図9)。
図9 リフロー前検査では検出できない不良
4. 最後に
本稿では、様々な電子基板の高品質化要求に合わせて進化を続ける『YSi-V 12M TypeHS2』の最新ソリューションとともに、急速に普及しつつあるリフロー前検査へのAOI活用事例とその改善効果を紹介した。
当社では、さらなる高い生産性、及び高い品質要求に応えられるように次世代3D AOIの開発も継続して行っている。
さらには、マウンタやSPIとのM2M連携機能も充実化し、ダッシュボードというSMTライン全体で生産、及び品質の見える化、分析を行うことができる新たなソフトウェアもリリースしている。
これからも当社は、SMT関連装置の業界随一となるトータルラインナップを活かした「1 Stop Smart Solution」により、お客様の生産性向上、及び高品質な生産を実現できるように貢献していきたいと考えている。
- 会社名
- ヤマハ発動機(株)
- 所在地
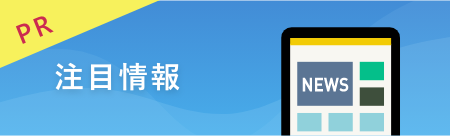
-
真空リフロー、N2リフロー、エアリフローのことなら、エイテックテクトロン(株)にお任せください。フラックスレス真空リフロー装置販売開始!エイテックテクトロン株式会社
-
独自の加工技術とノウハウで様々な材料にチャレンジ 〜色々なアイデアを生み出して研究者をサポート〜 ムソー工業株式会社 代表取締役 尾針 徹治 氏Gichoビジネスコミュニケーションズ株式会社
-
話題のGlass PKG実装技術の動向 〜先端電子部品への応用と 最新のCuダイレクトめっきGWCについて〜 Grand Joint Technology Ltd 大西 哲也(T. Onishi)Gichoビジネスコミュニケーションズ株式会社