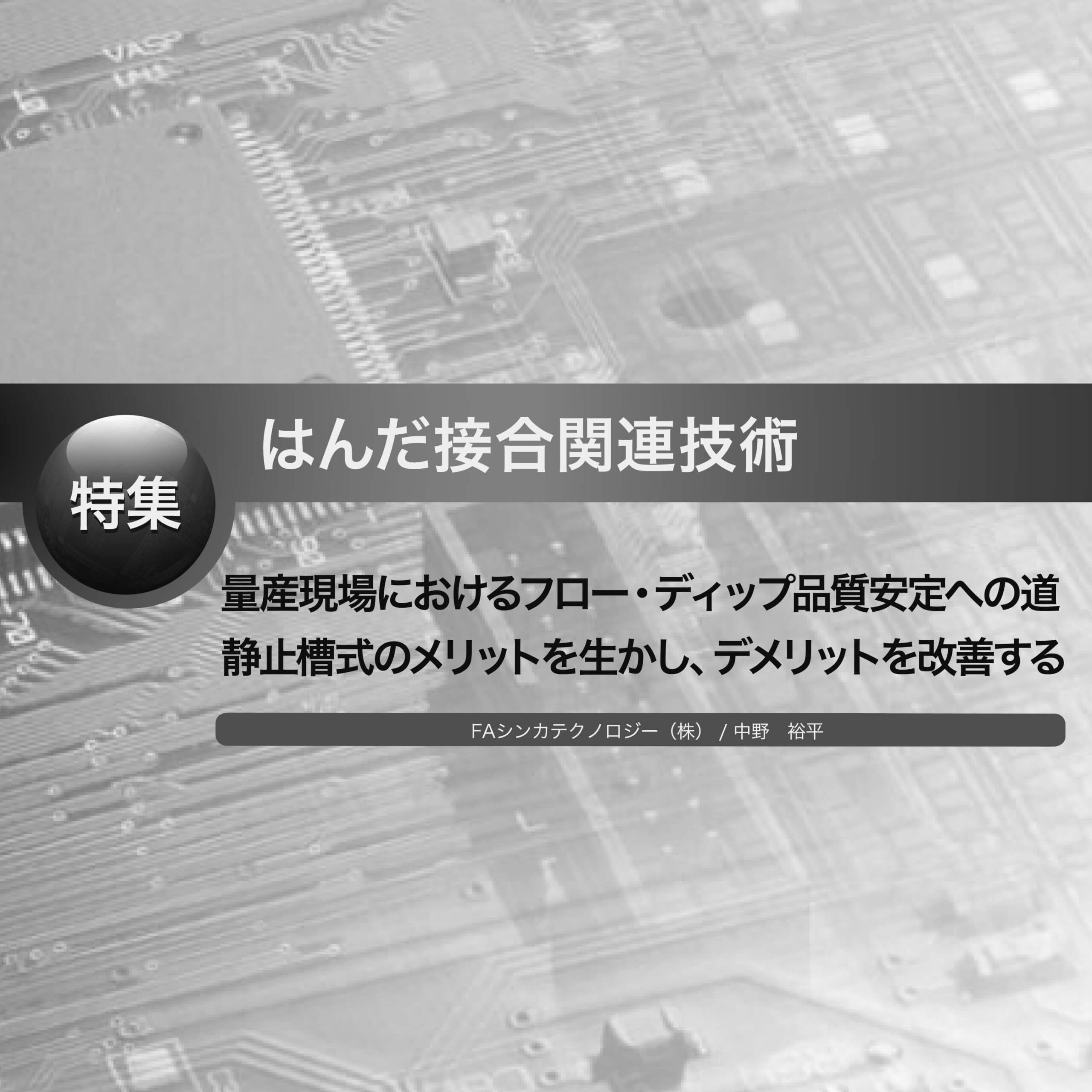
1. はじめに
近年、リフローなどの表面実装技術は飛躍的な進歩によって生産管理方法の確立、省人化が進むなど生産現場が変わりつつある。
さらに新型コロナウイルスの影響によってその体制の需要は多くなっているのではないだろうか。
その一方、挿入実装技術に関しては、SMD部品に置き換えられていく品種が増え、実装技術設備の進化は止まっているように感じる。
求められる品質や管理方法はSMTと同じであるにも関わらず、取り残されてしまっているこの技術に当社は注目し、開発、提供していくことで生産現場の支えになればと思う。
また、世界産業の基盤となる自動車産業ではEHV化が進み高電圧部品が搭載されていく。
それらは必ずTHD部品の仕事となり、挿入実装技術の進化の必要性は絶対であると確信してる。
2. 噴流槽式と静止槽式
挿入実装技術の歴史として、静止槽式(DIP)は古くからある技術ではないだろうか。
簡易的な槽に融解したはんだを溜め、そこに基板はんだ面を垂直方向から浸漬(DIP)、キャリア搬送を行いながら浸漬(ドラック方式)など、いずれもはんだ液面は静止した状態にあり、その為品質の再現性は良好な傾向にある。
この構造はシンプルで、メンテナンスの部位も少なく維持管理がしやすい工法となるが、その反面、静止状態にあるはんだ液は熱交換効率が悪いというデメリットを抱えている。
高温のはんだ液面に対し、浸漬する基板温度の差が大きい場合、温度の低い基板側に吸収されてしまい、はんだ温度が下がってしまうのである。
共晶はんだが主流だった時代は、固相線温度が低く、あまり影響はなかったが鉛フリーはんだが標準になってくると、そのデメリットは大きく影響し、現在では静止槽式での品質の確保は難しくなってしまい次第に減少。
それに代わり主流となっているのは融解したはんだを噴流させる噴流槽式で、今では数多くの種類がありいずれもはんだ液を常に流動させることで熱交換効率を良好にし、鉛フリーはんだでも品質を確保することが可能な工法である。
W噴流槽式
静止槽式
しかし、はんだ液を噴流させる為には複雑な構造を要し、メンテナンスや再現性の維持には人の技術は必要不可欠となっている。
3. 静止槽式+撹拌方式
そこで当社はなくなりつつある静止槽式のメリットに注目し、デメリットをカバーすることで品質の再現性と維持が可能になるのではないかと考え、試行錯誤を繰り返し、現在の撹拌方式にたどり着く。
改めて静止槽式におけるパレット搬送の交換効率の状態を確認すると、パレット搬送方式では、はんだ付け面以外をマスクすることでパレット開口部は噴流ノズルのような役割を担い、はんだ液面に浸漬することでその開口部へはんだ液が入り込むことではんだ付けを行うが、その際にはんだの熱は基板やパレットに奪われ、はんだ付けの品質に大きく影響を与える、これが静止槽式の熱の弱点といえる。
そこで温度の高いはんだをパレット開口部へ下から押し入れることで熱の循環を試みたが、基板と開口の中にあるはんだは押し上げるだけでは流動させることが出来ず滞留し、結果的に温度に変化は見られなかった。
つまり開口部に滞留する温度の低いはんだを開口部より逃がす必要性があった。
その逃がしに注目することで、当社の撹拌方式は完成した。
滞留する低い温度のはんだを逃がす引き波と温度の高いはんだを押し入れる波、その両方を担う方式が当社独自の撹拌方式となる。
さらに静止槽式本来のメリットであるメンテナンスの優位性を失わないよう、槽の中に特別な機構をもたない形で開発した。
静止槽
静止槽+撹拌方式
予熱、はんだ条件などは同条件にて(株)マルコム製『DS-10』にてデータ採取。
ともにはんだ温度ピークは変わらないが、静止槽のみの場合、パレット進入と同時に15℃近く温度ドロップしているのに対し、静止槽+撹拌方式では温度を維持しているのがわかる。
4. はんだ液面を捉える
品質の確保、安定において、融解したはんだを取り扱う静止槽式、噴流槽式その両方ともにはんだの液面の高さは重要な管理項目のひとつとなる。
噴流槽式の場合、噴流の高さはインペラの状態、噴流の速度、ノズルの状態やその高さの調整など様々な要素か関わることで品質を確保している。
その中にも噴流の高さを監視し、適度な噴流具合を調整出来るものも存在する。
では、はんだ液面が静止した状態にある静止槽式での管理はどのようにするのがいいのだろうか。
まず、はんだ液面の高さは当然重要となってくる。
従来は基板やガラスの板を実際に浸漬させ目視にて確認を行う方法など、人の手によるアナログな調整であった。
さらに重要となるのは基板とはんだ液面の平行状態である。
常に絶対水平であるはんだ液面に対し、基板の搬送状態は設備の設置や調整で合わせるしかなく、かなり難儀なものであると同時に、平行である保証はなかった。
そのはんだ液面の高さ、平行具合を監視する目的として当社ではオートレベリングという特許技術を取得し、はんだ液面対する基板搬送の傾きを補正する機能を開発。
また、その機能を転用し、はんだ液量の増減に対する浸漬の深さをを数値制御にて管理できるキャリブレーション機能も搭載した。
キャリブレーションピン。これをパレット搬送ロボット付近に設置することで液面を検出し、傾きや液面高さを数値として取り込む
(※左図)従来での理想とする水平状態
(※真ん中図)従来は搬送機の垂直動作は設備の姿勢によって決まるため、液面に対し水平にならない
(※右図)当社技術では、設備の姿勢に関わらず液面基準で水平になるように動作する
5. 付随するフラクサと予熱の数値管理
また、当社標準機である『FXM-1』はフラクサユニットを搭載し、そこではXY軸制御を採用。
塗布したい位置や塗布速度を数値にて指示、管理。
また、予熱に関してはゾーン送りを採用し、時間による温度管理を実現した。
展示する当社設備『FXM-1』
『FXM-1』設備構成簡略図
『FXM-1』のオプションとなるFXMツールによる条件設定画面。外部パソコン内で条件を数値で設定する。また、XY軸フラクサのポイント座標は図で描写可能
6. まとめ
これらの制御を行うことで人の技術は介在せず、数値のみでの品質の確保・管理を実現することを可能にした。
さらに標準機ではその数値データもオプションにて生産履歴記録をNASに取り込むことも可能にしている。
冒頭にも述べた表面実装技術の自動化までとはいかないかもしれないが、人の手をあまり必要とせず管理できる当社の技術は魅力的な設備であると自負している。
またメンテナンスを容易にすることで稼働率を上げ、生産量の増や、ランニングコストの削減といった副産物を得られたという声も多い。
ここで紹介させていただいた特許技術を取り入れた『FXM-1』は2021年1月19日(水)~20日(金)に東京ビックサイトで開催される「第36回 ネプコンジャパン」にて当社ブース内に実機展示を行うのでぜひご来場いただき、ご覧いただければと思う。
- 会社名
- FAシンカテクノロジー(株)
- 所在地
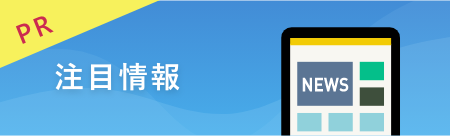
-
真空リフロー、N2リフロー、エアリフローのことなら、エイテックテクトロン(株)にお任せください。フラックスレス真空リフロー装置販売開始!エイテックテクトロン株式会社
-
独自の加工技術とノウハウで様々な材料にチャレンジ 〜色々なアイデアを生み出して研究者をサポート〜 ムソー工業株式会社 代表取締役 尾針 徹治 氏Gichoビジネスコミュニケーションズ株式会社
-
話題のGlass PKG実装技術の動向 〜先端電子部品への応用と 最新のCuダイレクトめっきGWCについて〜 Grand Joint Technology Ltd 大西 哲也(T. Onishi)Gichoビジネスコミュニケーションズ株式会社