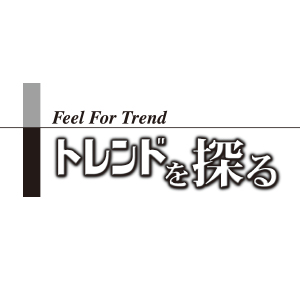
1. はじめに
プリント回路基板(PCB)の個片カット(デパネリング)は一般的にPCB実装組立ラインのプロセスチェーンの一番最後に行われる工程である。
デパネリングにより実装済みのプリント基板が大きなシート・パネルから分離され個片化される。
現状では実装済みPCBを分離するために刃物を使用した切断加工が選択されているが、精度向上、コスト削減、品質の要求が高まるにつれ新たな加工方法を選択する必要がでてきた。
特にレーザ加工によるデパネリングである。
本稿ではPCBデパネリング装置として、多くの導入実績を持ち、ドイツTier1にも採用されたLPKFレーザデパネリング技術を解説する。
2. 従来のプリント基板切断方法の利点と弱点
シンプルなPCB分割レイアウトの場合、ダイシング加工やルータ加工といった従来のプロセスが高速に加工できることもあり、最初の選択肢となる。
現在PCBを個片にするために使用されている加工技術の利点と弱点をまとめてみる。
■ダイパンチング
パンチ(凸型の工具)とダイ(凹型の工具)を組み合わせた金型により、PCBを打ち抜き加工する。
このプロセスはせん断の原理に基づいている。
ダイパンチングは大量生産に適した加工であり最初の選択肢になるが、基板レイアウトの変更ができないことや、機械的ストレスがPCBにかかることを想定しておく必要がある。
○利点……加工スピード 弱点:切断品質(バリなど)・金型コスト・加工ロットの安定・機械的ストレス
■ルータ加工
切削工具を回転させ、フライス加工によりPCBを切断するプロセス。
PCBへの機械的ストレスはかかる。
○利点……柔軟性(小ロットへの対応) 弱点:治具作成費用・粉塵・加工ロットの安定・機械的ストレス
■ダイシング加工
ダイシング加工による実装基板のカットはローラーブレードにて行われる。
この方式では直線のみの加工が可能であるが、機械的ストレスや発塵を気にしなければ大型かつ方形の回路基板を高速に加工することができる。
○利点……加工スピード 弱点:柔軟性(直線のみ)・粉塵・機械的ストレス
刃物を使用した機械加工は刃物の摩耗を考慮する必要があり、刃物の状態により加工品質は変化する。
また粉塵については追加のクリーニング工程を必要とし、機械的ストレスを緩和するためには一定の非実装面積を必要とする。
治具作成や位置合わせなどの段取りについても考慮する必要があり、多品種小ロットへの対応は比較的時間がかかる。
3. プリント基板レーザ技術
1.レーザ加工の原理
プリント基板へのレーザ加工というと、ビルドアップ基板に対する穴あけやレーザマーカによるマーキングがすぐに想定される。
フレキシブル基板に対してのレーザカットを想定される方もいるかもしれないが、PCBに対してのレーザカット、となると初めて聞かれる方も多いかもしれない。
レーザデパネリングではパルスレーザを使用する。
パルス毎に定量の材料が除去される(図1)。
図1 レーザデパネリングの加工工程
レーザを水平移動させることで加工が線になる。材料の切断は層ごとに行われることになり、 理論的には厚みのあるPCBでもレーザ切断処理できることになる。
リジッド基板、リジッドフレキシブル基板、フレキシブル基板の輪郭形状が複雑だったとしても、カットライン上にレーザを繰り返しあてることにより、切り取ることができる。
材料を層状に加工していく、というレーザの特徴を応用することも可能で、たとえば材料の表面のみ除去することで彫刻(マーキング)やザグリ(キャビティ)加工を行うことができ、複合材料の切断もできる。
2. レーザの種類
図2の表は一般的なPCB材料についてのレーザ吸収率を示したものである。
図2 PCB材料とレーザ吸収率
レーザの種類は波長によって呼び分けられており、波長が低いほうから、エキシマ(248nm)、UV(355nm)、グリーン(532nm)、IR(1064nm)、CO2(9.4μmと10.6μm)と代表的に分類される。
その中でもUVレーザは3種類すべての材料において比較的高い吸収率を保っている。
UVレーザよりもエキシマレーザのほうが各材料への吸収力は高いが、装置・ランニングコストが高額なため、PCBカット用途にはコストパフォーマンスの観点から使用することは推奨できない。
一方のCO2レーザは銅への吸収率がほぼなく、銅箔へのダイレクト加工はできないが、樹脂・ガラスへの吸収が良いことが示されている。
しかしながら、CO2のPCBカット例をみると、熱影響が強すぎて断面が強く焦げてしまい、基板表面から見ても、焦げが発生していることがわかるほどである(図3)。
図3 CO2レーザカット断面(上)とUVレーザカット断面(下)
レーザ波長をまとめると、UVレーザがもっともレーザデパネリングに適していることがわかる。
しかしながら、UVレーザといえども熱影響による材料の溶融がおきており、カット断面に焦げが残る現象を「0」にはできない。
この問題を解決するにはレーザ波長のみでなくレーザのパルス幅を見る必要が出てくる。
超短パルスのピコ秒、フェムト秒レーザを使用すると、非熱加工がおこなわれるため熱影響が少なくなることが現象として認められている。
LPKFではピコ秒レーザを応用した非熱加工の研究を行い、まったくカット断面に炭化が起きないCleanCut Technologyを開発した。
4. PCBレーザデパネリングの利点
レーザ技術にはさまざまな利点がある。
特に高密度実装を必要とする小さなPCBへのレーザデパネリングは非常に良い加工方法といえる。
レーザは金属薄膜ごとPCBを切断することができ、複雑な形状でも切断データを自由に作成・加工できる。
非接触加工となるので、PCBに対して機械的ストレスを与えることなく高密度実装基板を切断できる。
現時点でのLPKFレーザ装置による基板カットスピードはルータ加工と比べても遜色ないところまで速くなり、かつ切削粉がない(発塵しない)のでクリーニング工程が不要となる。
また、革新的なLPKF CleanCut Tehcnologyによりまったく炭化しないカット方法すら可能になっている。
■加工精度と加工断面
レーザビーム径が小さく、精密なXY制御が行われるため、寸法精度が良く高品質の加工結果が得られる。
さらに、レーザにより複合材料(例えばガラスクロスとエポキシ樹脂)が完全に切断されるので、非常に滑らかなカット断面を得ることができる。
CleanCut Technologyを使用すると、加工された断面にまったく炭化が出ない加工が可能となった(100%炭化なし)。
機械式基板カット方式と比較すると、レーザプロセスの精度、再現性、安定性により、はるかに高い信頼性が得られることになる。
■機械的ストレスのない加工
機械式基板カット方式とは対照的に、レーザによる非接触カットは機械的ストレスを基板に与えない。
そのため振動に敏感な電子部品の損傷がおこらない。
例えばセンサへのダメージによるプリント基板全体の故障、といった歩留まり低下も防いでくれる。
さらに、はんだ接合部への応力および基材の誘電特性への悪影響を防ぐことができる。
ストレスのないレーザデパネリングプロセスの利点は、ミリング加工と組み合わせて使用することもできる。
あらかじめPCBにV溝加工しておき実装後にレーザ切断することにより、PCBへの機械的ストレスが軽減されることになるため、結果として実装面積を増やすことができる。
■クリーンな加工
機械式基板カット方式では、加工中に粉塵が発生する。
LED基板や自動車用途基板においては粉塵を嫌うアプリケーションがあり、そのため徹底したクリーニング工程が必要となっている。
さらにエポキシ基板の粉塵は発がん性が認められており、環境負荷が高い。
それに比べるとレーザデパネリングは材料を気化し、発生したヒュームを吸引しながら加工することで発塵のない加工ができる。
これによって粉塵の堆積による潜在的な誤動作や性能低下が回避できることになる。
■材料の多様性
レーザデパネリングではレーザパラメータを変更することで、さまざまな基材を加工することができる。
別の材料を加工するからといって特別な金型や工具、専用のシステムは必要ない。
5Gに対応した高周波帯域で使用されるアプリケーションでは、フッ素系樹脂などの機械加工しづらい材料が使用されるが、これらの材料は機械的プロセスでは加工が制限される、もしくはランニングコストが高額になる。
レーザによる加工可能な他の材料には、金属(銅、アルミニウム、銀など)、樹脂(LCP、PTFEなど)、有機ガラス、およびセラミックがあげられる。
■設計自由度、材料費節約
機械式基板カット方式とは対照的に、レーザデパネリングではPCBの設計自由度に対する制限はない。
任意形状を加工できることと細いレーザビーム径により、どういった形状でも加工可能であり、カット部分と電子部品との間を最小化することができるので結果的に基板の高密度実装が可能になる。
ルータ加工のように最小半径、加工最小幅を考慮する必要もない。
レーザによるフルカットをすることでルータの加工しろを最小化すると、基板レイアウトによっては30%以上の基板材料を節約できることになる(図4)。
図4 LPKFレーザデパネリングによる材料コスト削減
基板材料の節約効果は小さなPCBにレーザデパネリングを使用するほど大きくなる。
レーザデパネリングを使用することでPCB設計をより効率的に行うことができる。
■柔軟性
レーザは切断以外にも広いアプリケーションに対応している。
同じレーザを使用しての穴あけ、マーキング、配線加工などが可能で、たとえばレーザシステムをカバーレイの加工などにも使用できる。
■長寿命
レーザによっては長年使用することで出力が低下することがわかってるが、ミリングヘッドやルータビットといった工具を交換する必要がないため、工具注文の手続きや関連コストが必要ない。
たとえば標準PCB材料の加工では約2000時間ごとにスピンドルを交換する必要があるといわれており、強度の高い材料ではさらに頻繁に交換が必要となる。
レーザの場合は、種類にもよるが35000時間以上の使用が認められている(数値として保証されるものではないことには注意)。
■トレーサビリティ
オプションで追加することができるトレーサビリティオプションは、
① 加工データログの取得
② 不良ボードの認識機能
③ 1D/2Dコードの読み込み/書き込み
④ デジタルレーザマーキング機能
が含まれており、PCBのトレーサビリティや多品種加工、海外での生産時にも応用可能である。
5. PCBレーザデパネリングの弱点
ここまでレーザ加工の利点を挙げてきたが、よくご質問いただく内容からレーザデパネリングの弱点について述べる。
■コスト
レーザデパネリングシステムへの投資は非常にコストがかかると考えられているが、実際には装置(とくにLPKF製)の価格レベルは、市場に出回っている標準的なフライス加工機のレベルに匹敵し、価格の面でも競争力がでてきた。
レーザシステムではモータヘッドや工具のコストが発生しない上に、前述した材料の節約により、コスト削減を実現できる。
レーザシステムの1時間当たりのコストは数百円と計算されている。
■高温加工
レーザカットの場合、PCBが非常に強く加熱され電子部品が損傷する可能性がある、という先入観があるかもしれない。
LPKFのレーザカットでの温度測定をしてみると、カット断面から100μmで65℃の熱しか発生しておらず、基板にかかる温度はリフロープロセスの約半分程度、ということになる。
その結果、電子部品やPCBの損傷はリフロープロセス中のような頻度では発生しない。
■加工スピード
事実として厚い基板になればなるほどレーザデパネリングは加工時間がかかる。
つまり加工スピードが遅い。
一方で薄い基板になればルータ加工に比べて速く加工できることがわかっている(図5)。
図5 レーザとルータの加工スピード比較
また、クリーニング工程(エアブローなど)が必要ないため、そのプロセスにかかる時間とコストを省いて考える必要がある。
■炭化問題
上記の高温加工に近いが、レーザデパネリングでは炭化の問題が避けられなかった。
炭化は材料加工中に生成される焦げによって引き起こされる。
レーザによって材料に誘導されたエネルギーが熱を発生させ、材料を溶融して気化させる。
加工プロセス中に特定の温度閾値を超えると材料が燃焼して炭素が放出される。
例えばFR4の温度閾値は350℃である。
レーザによる炭化は、ほとんどのレーザによるテストカットで引き続き発生しており、ユーザーに不利な印象を与えている。
加工時の不快なにおい、焦げによる絶縁信頼性への懸念、表面品質の低下、PCBの誤作動への懸念など。
実はこの焦げは、ある程度であれば許容できることが電気的な実験によりわかってきているし、見た目だけの問題、ととらえることもできるが、いまだその懸念は払しょくできていない。
LPKF CleanCut Technolgyは、これらの懸念を完全に払しょくする革新的なプロセスである。
この技術によってこれまで達成されえなかったクリーンで高品質なカット断面が得られる(図6)。
図6 LPKF CleanCut Technologyによるカット断面
切断面の元素分析を行った結果、炭化が全くないことが証明された。
しかもクリーニング工程などは一切必要としない。
クリーンで切削粉のないカット断面によりPCBの故障・不具合要因が減り、結果としてPCBの歩留まり向上に貢献する。
6. まとめ
従来の機械式加工技術よりも利点が多いレーザデパネリングがますます注目されるだろうと予測されており、それを裏付けるように次々と加工サンプルなどの評価依頼をいただいている。
特にLPKFによる最新レーザ技術開発のおかげで、従来の基板分割プロセスよりも技術的に優れているだけでなく、ルータ加工と比較した場合でも経済的にも魅力あるものになってきた。
さらにPCB基材や粉塵ごみを減らすことができるレーザデパネリングは環境負荷が低く、これからのPCB業界に求められる条件がそろっている。
すでに海外のEMSではUVレーザやピコ秒レーザを使用したPCBが多数生産されており、レーザデパネリングの優位性が実証されている。
特にコンシューマーエレクトロニクス、車載、医療用とといったハイテクアプリケーションではレーザデパネリングが第一の選択となるだろう。
<参考文献>
・上舘寛之, Patrick Stockbruegger:プリント配線板材料の開発と実装技術,初版,技術情報協会,633,2020
・シェーン・スタフォード:「UVレーザによるプリント回路基板の加工」,Industrial Laser Solutions Japan,September 2014,p16-19(2014.9)
- 会社名
- LPKF Laser&Electronics(株)
- 所在地
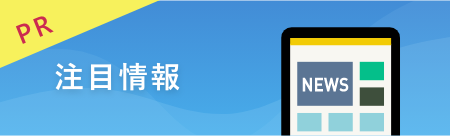
-
真空リフロー、N2リフロー、エアリフローのことなら、エイテックテクトロン(株)にお任せください。フラックスレス真空リフロー装置販売開始!エイテックテクトロン株式会社
-
独自の加工技術とノウハウで様々な材料にチャレンジ 〜色々なアイデアを生み出して研究者をサポート〜 ムソー工業株式会社 代表取締役 尾針 徹治 氏Gichoビジネスコミュニケーションズ株式会社
-
話題のGlass PKG実装技術の動向 〜先端電子部品への応用と 最新のCuダイレクトめっきGWCについて〜 Grand Joint Technology Ltd 大西 哲也(T. Onishi)Gichoビジネスコミュニケーションズ株式会社